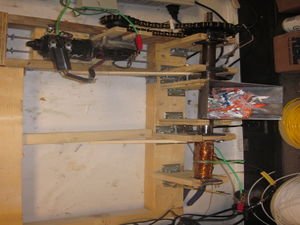
Nota: La tecnología de esta página ya no está actualizada; consulte la versión 2.3 de Recyclebot para obtener información actualizada.
A continuación se muestra un resumen modificado enviado para la presentación de Mech 461. Este proyecto representa el Recyclebot v2.
Los prototipos rápidos permiten fabricar productos o modelos a escala de forma rápida y precisa y son una herramienta útil de producción y diseño. Recientemente se ha desarrollado un modelo de código abierto, el RepRap, que se puede construir por menos de 1000 dólares, lo que amplía enormemente la base de usuarios potenciales de los prototipos rápidos. Podría utilizarse como herramienta de fabricación a pequeña escala o de desarrollo sostenible. La materia prima plástica del RepRap es un área en la que aún se pueden reducir los costes. Web4Deb ha creado un dispositivo que convierte los residuos plásticos en un medio de crecimiento para las plantas. Su dispositivo ha sido modificado para crear materia prima para la impresora RepRap. Se presenta una descripción y un análisis del diseño, incluidas las propiedades de los componentes, los procedimientos de prueba y los resultados de la extrusión. El éxito de este dispositivo mejoraría aún más la asequibilidad del RepRap al reducir los costes operativos. La producción de filamentos también podría ofrecer una fuente de ingresos alternativa. Además, permite el reciclaje de plástico en el hogar con un subproducto utilizable. Esto tiene implicaciones en el campo de la gestión de residuos, ya que el reciclaje en el hogar podría evitar las emisiones de gases de efecto invernadero y los costes económicos asociados a los programas de reciclaje municipales al evitar la recogida y el transporte de residuos.
Contenido
Resumen del proyecto
Como parte del curso de Ingeniería Mecánica de Queen's University, Mech 461, trabajaré en un dispositivo para convertir desechos plásticos domésticos en material utilizable para alimentar máquinas de creación rápida de prototipos a pequeña escala, como las máquinas RepRap , RapMan y Fab@home . A continuación se muestra la descripción oficial de este proyecto tal como se anuncia en el sitio web de Mech 461. <ref>Pearce, J. Descripción del proyecto: Diseño y prueba de una extrusora de residuos de plástico para un prototipo rápido de código abierto . Mec 461. [1] <ref>=== Introducción ===
Tradicionalmente, la impresión 3D se ha utilizado para la creación rápida de prototipos, donde las buenas tolerancias, la durabilidad y los tiempos de impresión rápidos dominan los requisitos del usuario. Por este motivo, las máquinas de creación rápida de prototipos comerciales se utilizan en muchas industrias para fabricar piezas personalizadas para productos en fase de diseño y pueden realizar operaciones como la impresión de un cojinete de bolas funcional utilizando voladizos y dos métodos de deposición de material. Recientemente, el desarrollo de prototipos rápidos de código abierto, como el RepRap, ha hecho que la creación rápida de prototipos sea lo suficientemente económica como para ser accesible para los usuarios domésticos y potencialmente útil para la tecnología apropiada de código abierto (OSAT). Las impresoras comerciales se destacan por producir rápidamente representaciones de alta tolerancia de piezas complejas; sin embargo, son mucho más caras (5000-200 000 dólares) que la RepRap de aproximadamente 1000 dólares. Además, como los prototipos rápidos patentados generalmente utilizan materias primas patentadas, también son extremadamente caros (entre 1 y 4 dólares por pulgada cuadrada), mientras que el plástico ABS, que se utiliza a menudo para el RepRap (www.reprap.org), es sorprendentemente más barato (0,032 dólares por pulgada cuadrada). El objetivo de este proyecto es impulsar aún más los prototipos rápidos de código abierto: utilizar plástico de desecho como materia prima en lugar de filamento ABS preformado.
Antecedentes científicos y de ingeniería
Recientemente se ha propuesto que las impresoras 3D de código abierto podrían utilizarse para impulsar el desarrollo sostenible<ref>J. M Pearce, C. Morris Blair, KJ Laciak, R. Andrews, A. Nosrat e I. Zelenika-Zovko, "Impresión 3-D de tecnologías apropiadas de código abierto para el desarrollo sostenible autodirigido", Journal of Sustainable Development 3(4 ), págs. 17-29 (2010). | http://www.ccsenet.org/journal/index.php/jsd/article/view/6984 <ref>. Para que esto sea realista, es fundamental que las materias primas se desarrollen a partir de materiales disponibles localmente para evitar la erosión de las ventajas de costos para la producción local. El uso de materiales disponibles localmente para fabricar OSAT no sólo garantiza que la comunidad en cuestión será menos dependiente de la ayuda extranjera si hay problemas con la tecnología, sino que también crea una sensación de empoderamiento, ya que la tecnología no se entrega como una forma de caridad. dependencia de la ayuda exterior. Esto se puede lograr mediante el uso de materias primas creadas a partir de productos de desecho (por ejemplo, bolsas o botellas de plástico) o mediante el uso de materiales locales disponibles, como los biopolímeros. La gran abundancia de plásticos en los desechos domésticos (incluidas bolsas, botellas, envases de alimentos y entretenimiento) es una realidad en la mayoría de las comunidades no rurales, pero estos desechos se pueden reutilizar. Se podría utilizar un proceso para crear un filamento de plástico de desecho para usar en RepRap. Por lo tanto, es necesaria una extrusora de plástico que pueda calentar los plásticos y extruirlos como un filamento que pueda ser utilizado por la impresora 3D. Cabe señalar que producir materia prima para filamentos es un desafío ya que el diámetro debe ser preciso y el filamento debe ser muy redondo (no ovalado) o la extrusora producirá piezas de mala calidad o se atascará, como ocurre a menudo cuando los propietarios de RapMan compran filamentos de repuesto. en la zona. Una extrusora diseñada con tolva puede no depender tanto de las propiedades de tamaño del material y también los avances confiables en el uso de material de alimentación en pellets combinado con un peletizador son otra opción que se puede explorar.
Objetivo de la investigación
El objetivo de este proyecto de investigación es diseñar, construir y probar una extrusora para RepRap que pueda tomar residuos de polímeros como materia prima.
Revisión de literatura
Siga este enlace para acceder al extrusor de residuos de plástico completo: revisión de la literatura . La revisión explora una variedad de literatura sobre temas de tecnología de creación rápida de prototipos de código abierto, manejo y reciclaje de residuos de plástico, propiedades de los materiales y tecnología de extrusión, entre otros.
Diseño
A continuación encontrará una descripción del diseño, incluidas instrucciones de montaje detalladas.
extrusora
El diseño de la extrusora de residuos de plástico está fuertemente influenciado por una extrusora desarrollada por "Web4Deb" (nombre de usuario en línea) que extruye HDPE para su uso como medio de crecimiento en acuaponía. Los detalles de este diseño se pueden encontrar en el blog de Web4Deb y en la página wiki RepRap del dispositivo . Se decidió que este diseño se usaría como base y se modificaría para producir un filamento de 3 mm para usar con la impresora 3D RepRap o RapMan.
El diseño tiene las siguientes características. Para más información consulte la sección Instrucciones de montaje .
- Tubo de 3/4" (diámetro interior) para cilindro extrusor.
- Dividido en 3 secciones individuales para ensamblar entre sí (engranaje, tolva y calefacción).
- Barrena de diámetro de barco de 3/4"-17" - insertada en el barril.
- Tolva soldada a la sección de la tolva. Plástico triturado insertado aquí.
- Barrena girada utilizando el motor del limpiaparabrisas (modelo usado de Dodge Neon 1994)
- Tren de transmisión de cadena y rueda dentada, relación 2:1 (reduce la velocidad, aumenta el par).
- conjunto de cojinete de empuje/arandela para restringir el movimiento en la dirección axial y contrarrestar la fuerza aplicada al sinfín al transportar el plástico.
- sección de calentamiento (descrita a continuación) y matriz con apertura de 3 mm.
Sección de calefacción
- Alambre de nicromo de calibre 14, enrollado alrededor del cañón. Asegurado con cinta Kapton resistente al calor.
- Se aplica cemento de horno al barril de la sección de calentamiento para evitar cortocircuitos. (se evita utilizando Nichrome aislado).
- alcanzó temperaturas de 225 ° C utilizando una fuente de alimentación para portátil de 15 V, 5 A.
- La cinta Kapton podría evitar cortocircuitos a través del cañón, pero está limitada a aplicaciones por debajo de los 250 ° C . Esta alta temperatura es necesaria si se extruye ABS o PET.
- La temperatura en el interior del barril calefactor tendía a retrasarse unos 30 ° C.
Se eligió un cable de calibre catorce en un esfuerzo por crear la zona de calentamiento con requisitos de energía mínimos. En la actualidad, se han logrado temperaturas de alambre de nicromo de 225 o C con 75 W de potencia (15 V, 5 A). La temperatura se puede ajustar modificando la corriente que pasa a través del cable de nicromo. Aumentar la corriente aumenta la temperatura del cable. Actualmente, la sección tiene solo una zona de calentamiento uniforme, sin embargo, se tomaron disposiciones para dos zonas de calentamiento en caso de que se considere beneficioso un calentamiento más gradual del plástico. Muchos procesos comerciales utilizan un calentamiento gradual para garantizar que el material se caliente de manera uniforme.<ref>Rosato, Dominick (1997). Plastics Processing Data Handbook (2nd Edition).. Springer - Verlag. (En línea)<ref> Este sitio web tiene especificaciones sobre la resistencia de cada calibre de cable y la corriente necesaria para calentar cada calibre a varios umbrales de temperatura.<ref> http://www.wiretron.com/design.html <ref>Los datos de este sitio se utilizaron para realizar los cálculos iniciales de diseño.
Actualmente, la sección de calefacción no está aislada; sin embargo, agregar aislamiento probablemente mejoraría el rendimiento. Se podría reducir el tiempo de calentamiento cuando la máquina se pone en marcha por primera vez y se podrían alcanzar temperaturas más altas en el cilindro del extrusor. Se podrían utilizar envolturas de fibra de vidrio/kevlar como aislamiento, al igual que guata de fibra de vidrio doméstica.
Listas de piezas
El diseño incluye varias modificaciones adicionales y piezas personalizadas. Se agregó una extensión de eje al motor del limpiaparabrisas para aumentar el diámetro del eje y proporcionar el espacio adecuado para el montaje de la rueda dentada. Se creó un collar para colocarlo entre el eje y la sección de engranajes para mantener el sinfín en su lugar y permitir el montaje de un cojinete de empuje. Cada una de estas piezas personalizadas se incluye en los dibujos a continuación.
El extrusor se construyó con una combinación de materiales de diseño personalizado y de stock. Los materiales de stock se resumen en la lista a continuación, junto con enlaces a sus proveedores.
Materiales en existencia:
Parte | Cantidad | Proveedor de ejemplo |
---|---|---|
Barrena para barco de 3/4"x17" | 1 | irwin |
Alambre de nicromo, calibre 14. | Rollo de 1-1/4 lb | McMaster-Carr |
Piñones - N.º de pieza: H40B12x1/2 y H40B24 | 2 | Corporación Ringball |
Cadena - Pieza#: 40-1R | 2 pies | Corporación Ringball |
Cojinete de empuje de agujas y arandelas - Pieza n.°: NTA815 y TRA815 | 1 rodamiento, 2 arandelas | koyo |
Tubería de 3/4" | mín. dieciséis" | Comprar online |
Chapa de metal de 1/2" | 1 hoja, 1 pie x 1 pie | Depósito de metales |
Cemento de horno | 100ml | Bomix Pyromix de BMR |
Pinzas de cocodrilo | 10 | La fuente |
Soportes de esquina | 10 | Hardware local |
cinta Kapton | 1 rollo de 3/8" x 36 yardas | Uline |
Varillas roscadas | 2 | Comprar online |
Motor del limpiaparabrisas | 1 | Se puede comprar usado, consultar eBay u otros. |
Trituradora de oficina | 1 | Grapas |
Arduino Uno | 1 | Arduino de RobotShop |
Cable USB compatible con Arduino | 1 | Phidgets, RobotShop |
Madera contrachapada | variable | Hardware local |
Madera | variable | Hardware local |
Sujetadores | variable | Hardware local |
Alambre de cobre | 2 pies | McMaster-Carr |
Todos los números de piezas enumerados fueron piezas utilizadas en los prototipos de extrusora. Se pueden sustituir otras marcas y piezas. Muchas de estas piezas pueden estar disponibles usadas o como desechos. Encontré muchas piezas gratis, como madera contrachapada y tablones de madera, sujetadores y algunas pinzas de cocodrilo. Las piezas enumeradas en cursiva son materiales que serían necesarios para el cuerpo del extrusor. En mi caso, estos materiales se incluyeron en los costos de mecanizado del Taller de Máquinas de Ingeniería Mecánica y de Materiales de la Universidad de Queen. Se requiere fabricación adicional para preparar las piezas para su montaje en la extrusora. Las herramientas necesarias deben poder cortar metal (es decir, amoladora, sierras, soplete de oxiacetileno, etc.) y realizar soldaduras simples. En mi caso estas piezas fueron hechas a medida como se explica a continuación.
Piezas personalizadas
Las piezas personalizadas se fabricaron en el Departamento de Mecánica y Materiales del Taller Mecánico de la Universidad de Queen. Agradecimientos especiales al Sr. Andy Bryson y su equipo por su ayuda en la fabricación. La mayoría de las piezas se fabricaron con el uso de equipos de soldadura, corte y perforación. En algunos casos, también se requirió un torno para la fabricación. Los archivos STL para cada una de las piezas personalizadas se pueden encontrar a continuación, así como los planos de fabricación de los componentes individuales. Los archivos muestran las dimensiones utilizadas para este extrusor en particular y se eligieron en función del extrusor Web4Deb precedente y para adaptarse a otros componentes (es decir, el sinfín). No se ha investigado la optimización de las dimensiones del extrusor.
Archivos de imagen de piezas
Extrusora de residuos de plástico: Limas
Instrucciones de montaje
A continuación se muestran las instrucciones para el montaje completo del diseño de extrusor que se creó como prototipo para el curso Mech 461:
Conjunto del cuerpo principal
El cuerpo principal consta de:
- Sección de calefacción, tolva y engranajes
- 6 x bridas
- morir
- placa de soporte de cojinete
- cuello
- cojinete de empuje y arandelas
- barrena
- piñón grande
Las piezas que se muestran en cursiva son piezas personalizadas. Los planos de construcción se pueden encontrar en la sección de archivos de piezas . La mayoría de estas piezas deberían poder construirse con herramientas de corte y perforación de metal. Sus dimensiones son las utilizadas para el prototipo del extrusor Mech 461, pero pueden modificarse para adaptarse a diseños individuales.
Una vez construida cada pieza se siguió el siguiente procedimiento:
- Se soldó una brida a cada extremo de las secciones de calentamiento, tolva y engranaje. Esto permite unir las secciones individuales. Tenerlas en secciones separadas permite trabajar en cada sección por separado del resto del cuerpo. En particular, es útil tener una zona de calentamiento separada en la que se pueda trabajar por separado y aislada del resto del conjunto del extrusor. Nota: Es probable que sea posible fabricar el extrusor con una construcción de un solo cuerpo.
- De la parte 1: Debe tener un subconjunto de engranaje, tolva y sección de calentamiento, que consta de las tuberías adecuadas y 2 bridas cada uno.
- La tolva estaba soldada a la sección abierta de tubería en la zona de la tolva.
- Se cortó un cuadrado de madera contrachapada, aproximadamente del tamaño de una brida. Se colocó entre la tolva y las secciones de calentamiento para reducir la transferencia de calor entre la zona de calentamiento y el área de la tolva. La sección de la tolva, la sección de calentamiento y la madera contrachapada se conectaron con sujetadores a través de los orificios de la brida.
- La matriz se puede conectar al otro extremo de la sección de calentamiento utilizando el mismo método.
- La barrena se inserta en el cilindro de la extrusora.
- El collar personalizado que se ve arriba se colocó en el vástago del sinfín. El collar está limitado por el aumento del diámetro del sinfín desde el vástago hasta la cuchilla. El diámetro exterior más pequeño del collar se coloca más cerca de la cuchilla del sinfín y encaja dentro del cilindro del extrusor. El diámetro exterior más grande limita el movimiento del sinfín axialmente hacia la zona de calentamiento, ya que es demasiado grande para caber en el cilindro del extrusor.
- A continuación se colocaron el cojinete de empuje de agujas y las arandelas en el sinfín (arandela, arandela de cojinete).
- El conjunto de cojinetes se sujetó con la "placa de soporte de cojinetes", que se conectó con sujetadores a la brida de la sección de engranajes. El cojinete de empuje compensa la fuerza axial ejercida sobre el sinfín cuando empuja el plástico.
- Se mecanizó una parte plana en el sinfín para proporcionar una mejor interfaz con el tornillo de fijación de la rueda dentada. Esto se consideró necesario durante las pruebas, ya que la rueda dentada se deslizaría sobre el vástago antes de que se creara la parte plana.
- Se colocó la rueda dentada grande en el vástago y se apretó el tornillo de fijación en la sección con la parte plana.
Esto completa el montaje del cuerpo principal del extrusor.
Sección de calefacción
La sección de calefacción incluye los siguientes componentes:
- Subconjunto de la sección de calefacción (consulte Conjunto del cuerpo principal )
- alambre de nicromo (aislado o no aislado)
- cinta Kapton
- alambre de cobre
- adaptadores de pinzas de cocodrilo
Si utiliza nicrom sin aislamiento :
- Cemento de horno
La construcción de la zona de calentamiento es un subconjunto bastante simple pero importante de la extrusora de residuos de plástico. El procedimiento difiere ligeramente si se utiliza alambre de nicrom aislado o no aislado. Si está utilizando un cable aislado , omita el paso 1 a continuación.
- Cubra el barril de la sección de calefacción (tubería) con una fina capa de cemento resistente a altas temperaturas. Yo usé Bomix Pyromix. Consulte la lista de componentes para obtener un enlace al producto. Haga la capa lo más delgada posible, pero asegúrese de que no quede metal desnudo.
- Envuelva el alambre de Nicromo alrededor del cañón de un extremo al otro. Una sección que cubra todo el cañón debería ser suficiente, pero dos zonas de calentamiento separadas pueden tener ventajas (calentamiento más gradual y uniforme; menos voltaje a través de cualquier cable determinado). Utilicé una zona de forma eficaz. Si está utilizando un cable sin aislamiento, asegúrese de que las bobinas no se toquen o provocarán un cortocircuito.
- Sujete el cable con cinta Kapton. La cinta Kapton tiene una clasificación de resistencia de 250 ° C. Si va a alcanzar temperaturas superiores a esta (necesarias para extruir ABS y PET), es posible que desee sellar el aparato con otra capa de cemento para hornos.
- Conecte el cable de cobre a las pinzas de cocodrilo y utilícelas como cables para conectarse a su fuente de alimentación.
- Pruebe y modifique según sea necesario.
Utilicé un adaptador de corriente de portátil antiguo (15 V 5 A) y alcancé los 225 ° C. La temperatura máxima se puede ajustar modificando la corriente que pasa por el cable. Esto se puede hacer añadiendo resistencia o cambiando las fuentes de alimentación. Se está trabajando en el futuro para desarrollar un sistema de microcontrolador para supervisar y controlar la temperatura. Esto se ha hecho en el pasado en el extrusor Web4Deb y en las boquillas de extrusión de la impresora 3D RepRap.
Estructura de soporte
La estructura de soporte consta de una base de madera con 8 soportes que limitan el movimiento axial, vertical y torsional del cuerpo del extrusor. Las instrucciones a continuación describen el proceso utilizado para crear el extrusor Mech 461. Gran parte de este diseño se puede modificar para satisfacer distintas necesidades. Este diseño ha pasado por algunas evoluciones. Se agregó un mayor soporte después de que uno de los soportes de madera se rompiera durante el uso. El tipo y la ubicación de los soportes también han cambiado. Los documentos de construcción para los diversos soportes se agregarán en un futuro cercano.
en curso
Sistema de transmisión
El sistema de tren motriz consta de los siguientes componentes:
- piñón grande y pequeño
- motor del limpiaparabrisas
- Extensión del eje (archivo de pieza disponible aquí )
- cadena
- dispositivo de tensiones
- 2 varillas roscadas de 1/4"-16"
- Tuercas de 8 1/4"
- soporte de madera
- flejes de metal
Todos estos componentes son de serie, excepto la extensión del eje, que se fabricó a medida. La rueda dentada grande también se modificó para reducir los diámetros de los orificios interior y exterior.
El montaje del sistema de transmisión se realizó siguiendo el procedimiento que se detalla a continuación. Próximamente se añadirán diagramas de construcción.
en curso
Molienda de plástico
Para que las botellas de plástico se pudieran convertir en materia prima viable mediante este método, primero había que triturarlas en trozos pequeños. Para ello se han investigado diversos métodos.
Siguiendo el trabajo de estudiantes de la Universidad de Delft, se probó la capacidad de trituración de varios electrodomésticos de cocina comunes.<ref>. Braanker, GB, Duwel, JEP, Flohil, JJ y Tokaya, GE (2010), "Desarrollo de un complemento de reciclaje de plásticos para la impresora 3D RepRap". (En línea) Disponible: http://web.archive.org/web/20200211171744/https://reprapdelft.files.wordpress.com/2010/04/reprap-granule-extruder-tudelft1.pdf (30 de junio de 2010) .<ref>Se probaron un procesador de alimentos, un molinillo de café y una licuadora, y la licuadora resultó ser la más eficiente. De acuerdo con el trabajo del grupo DelftU, se descubrió que la licuadora funcionaba mejor cuando se agregaba agua para mantener la máquina fría y contener el plástico que se estaba moliendo.
Sin embargo, esta solución no era lo suficientemente eficiente para triturar grandes cantidades, ya que requería demasiado tiempo. Además, el plástico triturado debía secarse antes de poder usarse en la extrusora. Se encontró un método más eficiente utilizando una destructora de oficina de la marca Staples®, diseñada para triturar tarjetas de crédito y discos compactos. Esto resultó ser mucho más eficiente en términos de tiempo y energía y evitó el uso de agua. Se encontró una destructora usada en un Value Village local por $24,99.
Las pruebas han demostrado que este método es suficiente. Se encontraron algunos problemas con las botellas de plástico más gruesas, ya que la trituradora no pudo cortarlas completamente en trozos pequeños. El borde cortante del sinfín aún pudo manipular la mayoría de estas muestras después de pasarlas por la trituradora. Para garantizar que la máquina funcionara sin problemas y extruyera a una velocidad constante, se utilizaron tijeras para cortar los trozos más grandes en trozos más pequeños antes de colocarlos en la tolva.
El método de preparación del plástico completo fue el siguiente:
- lavado de botellas de plastico
- Retirada de etiquetas y tapas
- Cortar en trozos manejables para la trituradora
- triturar
No se utilizaron manijas ni tapas porque no se podían introducir en la trituradora. Se alternaron los pasos de corte y trituración para garantizar que la trituradora no se sobrecalentara, como ocurrió con la trituración continua durante un período de 15 minutos. La trituración intermitente durante el transcurso de una hora no causó ningún problema con la trituradora.
El trabajo futuro debería centrarse en un dispositivo triturador que no requiera ningún corte de las botellas y que pueda producir trozos de plástico más pequeños que se alimentarán a la tolva.
Quizás una versión de escritorio de: https://www.youtube.com/watch?v=Aja7gcgRMJU funcionaría.
Pruebas
Se están realizando pruebas de extrusión y se está desarrollando una materia prima para filamentos de 3 mm que funcione. Próximamente se ofrecerán actualizaciones.
Trabajo futuro
Dispositivo de molienda
- Creación de un dispositivo de molienda de bajo coste y escala doméstica.
- debe moler las botellas en trozos pequeños (área < 1 cm 2 )
- No requiere corte previo
- Puede aceptar manijas, tapas, etc.
Ver también
- robot de reciclaje
- Categoría:Manual de recuperación de plásticos
- Controlador de código abierto para extrusora de polímeros
- Reproducir Rap
- Pruebas mecánicas de componentes de polímeros fabricados con la impresora 3D RepRap
- Desarrollo y viabilidad de aplicaciones para la impresora 3-D RepRap.
- Análisis del ciclo de vida del reciclaje distribuido de polímeros.
- Fabricación personalizada distribuida con energía solar
enlaces externos
- Robot de reciclaje RepRap wiki
- Adrian Bowyer: experimentos con extrusora de filamentos y extrusora de gránulos
- Blog de Capolight: más experimentos con extrusoras de HDPE granular
- Hilo de CNCZone
- Delft: experimentos exitosos de extrusión de HDPE
- Delft - Trabajo final de investigación
- Fab@Home: Extrusora a base de pellets , artículo de investigación
- Publicación número 1 de Forrest Higgs
- Publicación nº 2 de Forrest Higgs
- Libros de Gingery: Moldeador por inyección de plástico de bricolaje de Gingery , lista completa de libros de Gingery
- Extrusora alimentada por gravedad
- Lista de operadores de MakerBot [2] , [3] , [4] , [5] , [6]
- Operadores de MakerBot: todos los hilos de reciclaje
- Información sobre fabricación de polímeros/plásticos
- RecycleBot (extrusión de HDPE)
- Productos y Diseño Populares Sociedad Privada Limitada