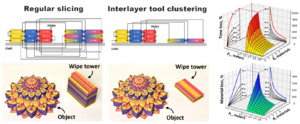
The most popular type of 3-D printing globally fuses plastic filament into a 3-D printed object. Historically, this has been done with only a single polymer. Advanced 3-D printer manufacturers now allow multiple materials and/or colors to be part of a single print. Presently in multi-material fused filament-based 3-D printing, significant amounts of waste material is produced. Each time a change from one material to another occurs, waste is produced through nozzle priming and/or purging. 3-D printing software (slicers) that prepare the g-code for multi-material 3-D printing typically change the material on each layer meaning that every layer, waste is generated often resulting in wipe towers with greater mass than the 3-D printed target object. An alternative fabrication approach based on interlayer tool clustering (ITC) is presented here for the first time, which is compatible with any commercial 3-D printer without the need for hardware modifications. The theoretical time, mass and energy savings are calculated and validated with a series of experiments to evaluate the proposed algorithm qualitatively and quantitatively. The results show the novel ITC method can significantly increase the efficiency of multi-material printing, with an average 1.7-fold reduction in material used, and an average 1.4-fold reduction in both time and 3-D printing energy use. In addition, this approach reduces the likelihood of technical failures in the manufacturing of the entire part by reducing the number of tool changes, or material transitions, on average by 2.4 times. These savings all support distributed recycling and additive manufacturing, which has both environmental and economic benefits, and increasing the number of colors in a 3-D print increases the savings and benefits.
- Free and open source code: https://github.com/apetsiuk/PrusaSlicer
3-D printing, additive manufacturing; open-source hardware; RepRap; multi-material, non-planar, Prusa, slicer, Slic3r, toolpath optimization
See also[edit | edit source]
- OS Computer Vision for Distributed Recycling and Additive Manufacturing
- Additional OS Computer Vision Applications
- Towards Smart Monitored AM: Open Source in-Situ Layer-wise 3D Printing Image Anomaly Detection Using Histograms of Oriented Gradients and a Physics-Based Rendering Engine
- Integrated Voltage—Current Monitoring and Control of Gas Metal Arc Weld Magnetic Ball-Jointed Open Source 3-D Printer
- Low-cost Open-Source Voltage and Current Monitor for Gas Metal Arc Weld 3-D Printing
- Slicer and process improvements for open-source GMAW-based metal 3-D printing
- Open-source Lab
- Open source 3-D printing of OSAT