Environmental Life Cycle Analysis of Manufacturing Options for Humanitarian Supplies: Drinking water containers
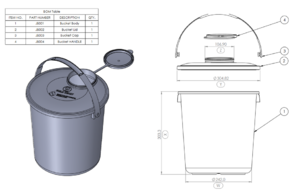
The purpose of this life cycle assessment study was to determine the life cycle impacts for production and distribution of a humanitarian supply item under various supply chain paradigms in order to illustrate the potential environmental benefits of organizing production and supply operations for these items in novel ways. To do this, a case study is used on a family-size water storage and dispensing bucket, such as the 14 L capacity polyethylene bucket commonly produced by Oxfam International. The LCA is a cradle to gate including production and transportation of PE plastic feedstock, fabrication of the water bucket, and transportation of the bucket to a common distribution site representative of a humanitarian aid location. Three different humanitarian aid locations are used to illustrate the range of potential impacts for each processing and supply system: Nepal, South Sudan, and Peru. Six processing and supply scenarios were investigated: (1) centralized Oxfam traditional system, (2) centralized commercial Chinese supply and distribution, (3) quasi-centralized Field Ready supply and distribution, (4) distributed supply and distribution system with 3-D printing, (5) distributed supply and distribution system with 3-D printing and local waste feedstock, and (6) distributed supply and distribution system with extrusion molding and local waste feedstock. The results found the major contribution to total GHG emissions are electricity usage for manufacturing and shipping feedstock and final product. Among Systems 1–3, System 1 and System 2 are environmentally poor as the electricity emissions in Pakistan and China are high. System 3 was an improvement as the products are manufactured locally. Decentralized supply and distribution system with 3-D printing (System 4) is less compatible with regions of high grid emissions. In System 5, the same equipment has been used, but with local waste feedstock, which shows an improvement of 67.7% for Nepal and 65.5% for Peru because of the reduced shipping emissions, even if the manufacturing emission is the highest among all of the systems. System 6 is feasible for all three locations. It is concluded that manufacturing should be prioritized on grids where the electricity emission is lower using local waste feedstock as it is the most efficient approach; however, a further study should be done on operating the FPF/FGF 3-D printer or extrusion molding systems powered with distributed photovoltaic systems in order to complement this process and produce the most environmentally responsible production.
See also[edit | edit source]
- Is small or big solar better for the environment? Comparative life cycle assessment of solar photovoltaic rooftop vs. ground‑mounted systems
- Life cycle assessment of pasture-based agrivoltaic systems: Emissions and energy use of integrated rabbit production
- The Greenest Solar Power? Life Cycle Assessment of Foam-Based Flexible Floatovoltaics
- Greener Sheep: Life Cycle Analysis of Integrated Sheep Agrivoltatic Systems
- Life cycle analysis of silane recycling in amorphous silicon-based solar photovoltaic manufacturing