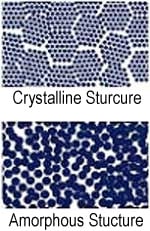
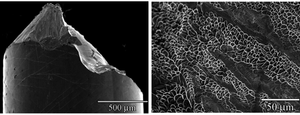
アモルファス金属は、 その非晶質の原子構造にちなんで名付けられました。そのため、この材料には結晶構造がありません。アモルファス原子構造はガラスの特徴であるため、この材料は金属ガラスと呼ばれることがあります。アモルファス構造とは、金属内の原子の無秩序な配列を指します。 [ 1]一般に、結晶性金属よりも硬度、降伏応力、破壊応力が高く、弾性率と剛性率も同等です。強度は、結晶構造による粒界すべり面がないことによるものです。[ 2 ]
歴史
アモルファス金属構造は、1950年代に鉛箔をおよそ10 12 K/s(ケルビン毎秒)の速度で急冷したときに発見されました。これにより、凝固中の結晶化が回避され、金属の液体状態で存在していた原子のアモルファス配列が維持されました。部品を冷却するには周囲への熱の放散が必要なので、部品の形状が急速冷却能力に大きく影響します。アモルファス構造の形成は、約50µmの厚さの箔に限定されていました。[3]しかし、このプロセスによって達成された金属のユニークな特性は、主にガラスの特徴であるアモルファス原子構造のために、新しいクラスの材料、金属ガラスの作成を正当化しました。プロセスと材料の進歩により、すぐに数センチメートルの厚さのバルク金属ガラス(BMG)の形成が起こりました。 1969年、チェンとターンブルは臨界冷却速度100~1000°K/sで直径0.5mmのPd77.5Cu6Si16.5の非晶質球を形成した。[ 4 ]
形にする
金属ガラスの形成に寄与する主な原理は、急速な冷却速度です。融点Wからの冷却速度が長いほど、原子が結晶に整列する時間が長くなるため、粒子が大きくなります。冷却速度が増加すると、粒子が非常に小さくなるだけでなく、すぐに存在しなくなります。金属の液体状態で存在していた原子の非晶質配置は保存されます。[4]
非晶質構造の形成の鍵は結晶の形成を防ぐことであると思われるため、この目的は、金属結合W自体を形成する力を妨害することで直接対処できます。サイズが大きく異なる金属は結合しにくいため、それらを含む合金は結晶化に時間がかかります。同じ合金にさまざまな原子半径がこのように配置されていることを「混乱原理」と呼びます。 [4]ガラスが形成されるには、異なる金属の原子半径が少なくとも 12% 異なっている必要があります。 [5]ジルコニウムW、アルミニウムW、ニッケルW、銅Wなどの一連の元素を含む合金は、1 K/s という低い臨界冷却速度に達することができます。臨界冷却速度とは、アモルファス構造を達成できる最低の冷却速度を指します。[6]
ガラスの形成を促進するための追加の戦略は、融点 (T m ) とガラス転移|ガラス形成温度W (T g ) に基づいて合金の組成を選択することです。合金の T mが低くT gが高いほど、2 つの温度の差が小さくなり、したがって、潜在的に低い冷却速度でガラスを形成するために必要な時間が短くなります。BMG の形成に関連する温度は、表 1 に概説されています。 [2]
![]() |
表1:選択されたBMGの温度とロッド直径に関するガラス形成能力。[2] |
金属ガラスを製造する最初の方法の 1 つであるメルトスピニングは、1000 °K/s を超える冷却速度を達成しました。これは、ガラス形成にそのような速度を必要とする合金には必須でした。この方法は、高速回転するドラムに溶融金属の流れを注ぐというものでした。ドラムは液体窒素で内部冷却されていました。ドラムが高速回転するため、ドラム上に金属を薄く短時間で塗布することができました。伝導冷却法を使用すれば、薄い量の金属をそのように素早く冷却することが可能でした。
最近の合金では、このような高い冷却速度は必要ありません。この特性により、鋳型の壁によって十分な冷却が行えるため、鋳造が可能になります。液体窒素は、鋳型の壁を冷却するための強力な手段として使用できます。熱は金属の外面によってのみ消散されるため、冷却は依然として金属部品の形状に大きく依存します。
図 3 に示すように、非晶質状態の形成は、冷却曲線 (たとえば青い線) が結晶ノーズを「逃す」能力です。図 4 に示すように、融点 (プロットに示されている T 1 ) を下げ、ガラス形成温度を上げるか維持すると、冷却曲線の傾斜が小さくなり、したがって冷却速度が低下し、結晶ノーズを逃します。[3]
![]() | ![]() |
図3: 冷却図。 [3] | 図4:より低い融点を示す冷却図。 [3] |
機械的性質
これらのガラスの非晶質構造により、結晶粒Wおよび粒界 Wを持つ材料に通常存在する滑り面Wが欠如しています。その結果、金属ガラスは結晶性金属よりもはるかに大きな変形抵抗 W を示します。この特性により、一般にビッカース硬度 W (H v )、降伏応力 W (σ Y )、破壊応力 W (σ f ) が大幅に増加します (表2を参照)。その他の特性として、弾性係数W (E)、せん断剛性係数 W (G)、体積弾性率 W (K)、ポアソン比 W (v ) があり、これらは既存の他のエンジニアリング材料と同等です。 [2]
![]() |
表2: BMGの圧縮試験から得られた応力-ひずみ曲線パラメータ。 [2] |
粒界は、必要な化学反応が起こるための表面積を増やすため、腐食の弱点でもあります。BMGには粒界がないため、腐食しにくいです。 [7]
比較のために、いくつかの一般的なエンジニアリング材料の特性を表 3 に示します。
![]() |
表3:一般的な工学材料の特性[8] |
表2で調べた鉄系BMGは、チタンTi-6Al-4Vの約3倍の降伏応力を持ち、同等の弾性係数と剛性を持つ構造用鋼A36の10倍以上の降伏応力を持っていることは明らかです。[8] 降伏応力が高く、したがって変形に対する耐性が高いため、金属ガラスは非常に高い弾性と機械的エネルギーを蓄える能力を持っています。[4]
BMGは硬いため、延性が低く、引張強度も低いと考えられています。大きな引張荷重がかかると、局所的なせん断の結果としてせん断帯と呼ばれる現象が発生します。[7]
成形方法
ダイカスト
鉄などの材料をダイカストすると、冷却過程で正味の体積が大幅に減少し、不正確な部品が生成されるため、後で表面仕上げが必要になります。金属ガラス部品のダイカストは、収縮がほとんどないため非常に実用的です。これには主に2つの理由があります。第1に、ガラスの形成は、ガラス内の原子の配列が液体と同じになるように行われるため、本質的に相転移はありません。原子が再配置されないため、ダイの体積は変化せず、したがって収縮はありません。第2に、低いT mを持つ合金は、たとえばほとんどの炭素鋼よりも冷却が少なくて済みます。温度変化が小さいため、冷却中の収縮も少なくなります。金属ガラスのこれらの特性により、鋳造後に表面仕上げをほとんど必要とせずに、ニアネットシェイプのダイカスト部品が得られます。 [3]
熱可塑性成形
![]() |
図2:BMGの熱可塑性成形に関与する要素の大まかな概略図。 [9] |
BMG は、熱可塑性成形によって比較的複雑な形状に成形できます。ガラスの温度が T gよりわずかに高い場合、ガラスは十分に可塑性があり、破損することなく変形できます。金属ガラスのインゴットWは、図 2 に示すように金型に押し込まれます。成形プロセスは T gより上で行われるため、ガラスは固まっておらず、この温度で長時間放置すると結晶化する可能性があります。BMG の特定の合金は結晶化に対して十分に耐性があるため、熱可塑性成形プロセスを実行するのに十分な時間があり、部品の望ましい特性を維持できます。BMG はより小さな形状に制限されることはわかっていますが、冷却中の収縮も低いです。これらの特性により、熱可塑性成形は小型部品の成形に適用できます。部品の成形に必要な平均圧力は、ハーゲン・ポアズイユの式で表されます。[9]
Lはチャネルの長さ、dは直径、ηはBMGの粘度、νはチャネルを移動する速度、pはプロセスに必要な圧力です。モデルによれば、実現可能な最大成形圧力と最小フィーチャ直径は約300MPaと10nmです。[9]
プロセスエネルギーの削減
アモルファス金属の製造に必要なエネルギーを削減する最も明白な方法は、より低い融点を持つ金属を作ることです。融点が低ければ、金属を適切な温度まで加熱するのに必要なエネルギーが少なくて済みます。逆に、より低い融点によって金属を急速に冷却するプロセスのエネルギー効率は向上します。これは、より小さな温度差で金属を冷却するのに必要なエネルギーが少なくなるためです。融点が低いと臨界冷却速度が遅くなる可能性が高くなり、冷却の効果をより周囲温度に与えることができます。従来の急冷法で達成されるよりも速い冷却速度を達成するには、かなりの量のエネルギーを強制的に冷却する必要があります。臨界冷却速度を低下させることは、主に前述の理由によりエネルギー消費を削減します。
BMG の製造プロセスにスクイーズ鋳造法を導入すると、効率を高めることができます。スクイーズ鋳造法は、基本的に 100Mpa 程度の圧力で鋳造プロセスを実行します。凝固中、高圧により液体金属はプロセス全体を通じて鋳型壁と接触し続けます。鋳型壁は材料を冷却します。これにより熱除去の効率が向上し、達成可能な冷却速度が増加します。金属の融点とガラス形成温度は、圧力が高くなると上昇します。したがって、金属を低圧で溶かし、圧力を上げて鋳造すると、冷却プロセスで達成しなければならない温度差が本質的に減少します。[10]
熱可塑性成形プロセスの効率を上げる方法は、ハーゲン・ポアズイユの式を調べることで仮説を立てることができます。プロセスの速度を上げ、必要な圧力を下げるか維持すれば、効率を上げることができます。速度が速いほど熱可塑性成形プロセスに必要な時間が短縮され、材料の最終形状が確立された後の冷却プロセスに多くの時間を費やすことができます。これは、成形する部品の形状を変更することで簡単に実現できます。圧力を維持しながら長さを短くし、直径を大きくすると、成形プロセスの速度が上がります。部品上の特徴の量と複雑さを減らすと、直径を大きくするのと同じ効果が得られます。プロセス中の金属の粘度を下げると、効率が向上します。これは、金属の組成を粘性の低い金属に変更するか、ガラス成形温度にできるだけ近い温度でプロセスを実行することで実現できます。 [9]
制限事項
金属ガラスにはいくつかの優れた特性があるにもかかわらず、この材料には依然としていくつかの限界があります。強度が高いため、一般的に弾性ひずみ限界は低くなります。材料は負荷がかかっても変形しませんが、破壊応力に達すると壊滅的に破損します。材料が破損しそうになっても視覚的な手がかりがほとんどないため、構造用途では危険です。
金属ガラスの形成は、実用的ではない薄い箔から直径数センチの最新の BMG に進化しましたが、依然として厚さが薄く形状が不自然な部品に限られています。
金属ガラスを製造するためのさまざまなプロセスはまだ初期段階にあるため、この材料の採用と生産はまだ広く普及していません。製造コストは従来の結晶合金よりもはるかに高いため、用途が限られています。プロセスのスケールアップに対応するために施設が拡張されるにつれて、このプロセスは将来的に経済的に実現可能になる可能性があります。今日の鋼鉄などの大量生産材料と同様に、BMG をこのように大量に生産すると、小規模生産に関連する製品単位あたりの間接費の多くを相殺できる可能性があります。
金属ガラスは、ガラス形成温度が低いという特徴があるため、低温用途に限られています。ガラス形成温度を超える環境に置かれると、非晶質特性を失い、結晶性金属に再形成される可能性があります。[7]
アプリケーション
金属ガラスは、コストに関係なく、製品に使用した場合の性能向上が正当化されるハイエンド市場での用途が見出されています。剛性、硬度、ひいては傷への耐性により、ハイエンド電子機器のケースとして使用され始めています。硬度が高いため、工具に使用するのに最適です。粒子構造がないため、原子を超える長さスケールがないため、刃を非常に鋭く研ぐことができます。この特性はナイフ、特にメスに有効です。
単位体積および質量あたりの弾性エネルギー貯蔵量が高く、減衰率が低いため、金属ガラスはバネとして使用できます。ゴルフクラブや野球のバットなどのスポーツ用具は、高硬度と弾性エネルギー特性を利用して、発射体へのエネルギー伝達を良好にしています。この特性が活用されているゴルフクラブのヘッドやテニスラケットのフレームに効果的に使用されています。デバイスにおけるバネのその他の用途としては、高速リレーがあります。
情報の保存と再生には、粒子構造がないことと硬度が高いことが利用されます。原子レベルに近い特徴を金属ガラスの表面に成形またはエッチングして、超高密度デジタルデータを再現するためのマスターを作成することができます。[7]
小型部品はダイカストでほぼネットシェイプの製造が可能で、その形状を実現するために追加の機械加工を行うとコストがかかり非現実的です。[4]
参考文献
- ↑ジャンプアップ:1.0 1.1 「テクノロジー Liquidmetal Technologies」 Liquidmetal Technologies。Np、nd Sat. 07 Nov. 2009.; http://web.archive.org/web/20110518094601/http://www.liquidmetal.com:80/technology/default.asp ;
- ↑ジャンプアップ:2.0 2.1 2.2 2.3 2.4 2.5 Gu, X., Poon, SJ, Shiflet, GJ, Widom, M. (2008). アモルファス鋼の延性向上: せん断弾性係数と電子構造の役割. Acta Materialia, 56, 88-94.
- ↑ジャンプアップ:3.0 3.1 3.2 3.3 3.4 Schroers, J., Paton, N. (2006). 「アモルファス金属合金はプラスチックのように形成される」 Advance Materials Processes、2006 年 1 月、61-63 ページ。
- ↑ジャンプアップ:4.0 4.1 4.2 4.3 4.4 Telford, M. (2004). バルク金属ガラスの事例 Materials Today, 2004 年 3 月, 36-43 ページ。
- ↑ Lee, H., Cagin, T., Johnson, WL, Goddard III, WA (2003). 金属ガラスの形成基準:原子サイズ比の役割。Jornal Of Chemical Pysics, 119(18), 9858-9870.
- ↑ Telford, M. (2004). バルク金属ガラスの事例 Materials Today, 2004年3月, 36-43.
- ↑ジャンプアップ:7.0 7.1 7.2 7.3 Ashby, M., Greer, A. (2006). 構造材料としての金属ガラスScripta Materialia, 54, 321-326.
- ↑ジャンプアップ:8.0 8.1 R.C. Hibbeler、「材料力学」、第 3 版、Prentice Hall、1997 年。
- ↑ジャンプアップ:9.0 9.1 9.2 9.3 Schroers, J., Pham, Q., Desai, A. (2007). バルク金属ガラスの熱可塑性成形 - MEMS および微細構造製造のための技術。Journal of Microelectromechanical Systems、16(2)、240-247。
- ↑ Kang, HG, Park, ES, Kim, WT, Kim, DH, Cho, HK (2000). スクイーズ鋳造法によるバルクMg-Cu-Ag-Yガラス合金の製造。Materials Transactions, 41(7), 846-849. 2009年11月9日閲覧、日本金属学会データベースより。