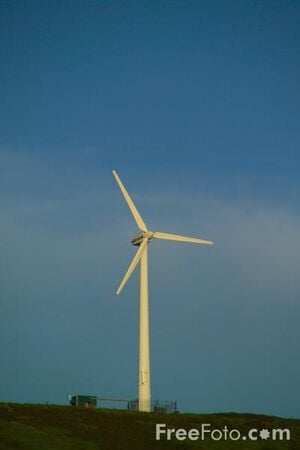
Wind PowerW is a prominent "green" solution to the global energy crisis. Wind power was the most rapid growing source of usable energy from 1990-2002[1] in 2003, and its strong growth continues. Currently the majority of wind farms are in European countries and the United States. The global wind power capacity by the end of 2008 had reached a value of over 120.8 GW.[2] The Wolfe Island Wind Farm, located in Ontario, Canada just finished the construction of 86 wind turbines, each with a 2,300KW rating, establishing an overall power capacity of 197.8MW for the farm.[3] The average life span for the blades of a wind turbine is approximately 20-25 years. Because of the current rapid growth it can be expected that thousands of turbine blades will need to be discommissioned within the next 20 years.]
There are currently three options for the disposal of the blade:landfill, incineration and recyling.[4]Landfill disposal represents the cheapest option; however most countries aim to reduce the amount of landfill waste, and in the future disposal of such a large amount of material will be unacceptable. Turbine Blades are constructed from composite materialsW and these can be burned for calorific value[5] as a source of energy. Incineration can lead to the production of hazardous by-products and approximately 60% material remains as scrap[4] which will be disposed of in a landfill, or recycled as construction filler within a material. Currently, there are two main methods of recycling: mechanical, which greatly reduces the scrap's size to produce recyclates, and thermal processing,[5] which breaks down the scrap material into materials and energy.
Future materials options must be considered within the blade design to increase sustainability. Research is being conducted into the use of thermoplasticW polymers which are a more sustainable option than the current thermoset polymer material.[4]
Background: Wind Turbine Blades[edit | edit source]
The basic structure of a wind turbine consists of a rotor supported by a tall base with three cantilevered rotor blades attached. The hub height averages at about 90 meters, and the rotor blades can range from 45 to 90 meters.[4] There are two main loads that are applied to the blades: the applied force due to wind, and the gravitational weight from the mass of the blade.
Materials Requirements[edit | edit source]
To reduce the effect of gravitational forces, and to obtain optimal aerodynamic performance, a material with a low density and high stiffness must be utilized.[5] A long fatigue life is also important to reduce material degradation. Figure 2.0 displays a graph of stiffness vs. density for different materials.
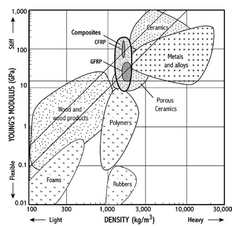
Composites are the best option for rotor blades as these have the best balance between stiffness and density for the application (see Figure 2.0). Composites are the most commonly used material in the wind power industry.[5] Composite materials consist of the formation of two materials with very different properties.[6] Commonly the composite material will be made up of a matrix with provides toughness and supports the fibers within. The fibers add tensile strength to the material and are the dominant contributor to the properties of the composite.[5] Different mixing ratios and combinations can be employed to provide different desired results. The Stiffness of the composite can be determined according to Equation 1.[5] Stiffness Equation (1): Ec = η * Vf + Vm * Em[7]
Where Vf and Vm represent the molar volumes of the fiber and the matrix, and n represents the orientation factor. From this equation it can be seen that the stiffness of a composite material is dependent on the stiffness of the polymer matrix, and the orientation of the fibers.
Current Materials[edit | edit source]
Composites that are used for wind turbines mainly use a glass or carbon fiber reinforcement in a polymer matrix. The most common design is a thermoset matrix with glass fibers.[1] Although the properties of glass reinforcement are not as good as carbon (see Table 1.0) but they provide similar reinforcement at a reduced cost. ThermosetW polymers are cross-linkedW meaning that they undergo an irreversible curing process[8]making recycling methods quite complicated.
Recycling[edit | edit source]
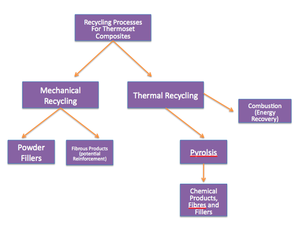
Two common methods of recycling thermoset composites are mechanical and thermal processes. A schematic of the different Recycling Process can be shown by Figure 3.0.
Mechanical Recycling[edit | edit source]
The mechanical recycling process of wind turbine blades is quite simple, and can be described within a three step system:
- Wind turbine blades are removed from the base and cut into smaller sizes on location for easier transport.[4]
- A crushing/hammer phase reduces the the size of the pieces to 10 millimeters to less than 50 micrometers in size.[8]This process "pounds" the resin out of the fibers.
- A grading process is used to separate the larger/courser pieces (fiber) of recyclate from the smaller finer grains which consist of the fillerW and polymer material.
The finer sized recyclate (polymer/filler material) can be used as a substitute of a filler material for another application. A benefit of this is that the recyclate is a much lower density than most common fill materials, and when 10% of a filer material is replaced with recyclate it can reduce the mass by up to 5%. However the addition of a recyclate as a substitute of a filler material will result in a reduction in the mechanical properties. This is because the recyclate absorbs more resin (matrix material) than most filler materials which leads to a higher viscosity mould. This reduction is tolerable only for anything less than a 10% loading situation.[8]
Research has attempted to utilize the coarse fiber component of the recyclate for reinforcement purposes in applications. Substitutions of small additions of fiber recyclates have been observed to cause large reductions in strength and toughness.[4]One of the main causes of this decrease in strength is due to the fact that there will always be some residual resin remaining on the recyclate fibers that makes it difficult for the fiber to bond with the new polymer matrix. Although not recommended by most scientists to introduce this recyclate material into the high end industry; applications in the construction industry are currently being investigated. For example, recyclate can be used as an alternative to wood fiber in particle board, or even as reinforcement in asphalt.[8]
Thermal Recycling[edit | edit source]
Combustion of Old Turbine Blades[edit | edit source]
Energy can be obtained from burning thermosetting polymers. Most resins have a calorific value of 30,000KJ/Kg.[7] The calorific value of a composite material is mainly dependent on the polymer potion. This is due to the fact that most filler and fiber material is incombustible. Some filler materials are even manufactured to absorb energy such as alumina trihydrate, which absorbs 100KJ/Kg when heated.[7] After the polymer components have been burned off, the remaining scrap can be used in cement application.[7]
Pyrolysis Processing of Old Turbine Blades[edit | edit source]
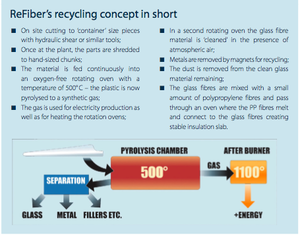
PyrolysisW focuses on the recovery of the energy content within the polymer. Processing by a method of Pyrolysis is when a combustible material is heated to around 500 °C without oxygen, causing it to break down into lower weight organic solid substances or liquid hydrocarbonW products such as gas. The effect of this process on the glass fibers is much higher in the case of glass reinforcement fibers than carbon fibers. Although both fibers maintain their stiffness the glass fibers loose 50% of their initial strength, and the carbon fibers loose only 5% of their strength. In the case of glass the left over fibers can be used in applications such as fiber reinforcement in glue, paints or concrete. Since the carbon fibers have such a small reduction in strength they can be reintroduced as reinforcement in low risk composite materials. The energy, which is harvested from polymers, can be used to generate electricity.[9]
Refiber Aps is a company in Denmark, which has taken this process and developed it for the wind turbine industry.[9] Figure 4.0 represents their recycling process.
Feasibility of Recycling of Turbine Blades[edit | edit source]
Although current popular recycling options for the turbine blades are a better option than landfill there are still many issues. It has been less than twenty years since harvesting wind power on a large commercial scale has become popular, and because of this the wind turbines have not experienced a full life cycle. Currently, there is not a large supply of composite waste for commercial recycling companies to be prosperous; this corresponds to less economic incentive for scientific developments in the wind turbine recycling industry. However, it is important that these recycling techniques are developed because it can be expected that there will be a large turn-over of wind turbines within the next 10-15 years and the industry should be prepared.
From the discussed options of current recycling technology it can be observed that recycling does not provide the best solution when trying to develop a sustainable life cycle for the wind turbine blade. Although it is important that recycling is considered for the blades which are already manufactured; it is important to now consider building a more sustainable wind turbine blade with new and different materials to make disposal and recycling processes easier in the future.
Future Materials and Manufacturing Processes[edit | edit source]
Thermoplastic Composites[edit | edit source]
It is important to consider future materials in the manufacturing of the wind turbines, in order to increase the efficiency of recycling. One current and popular option is the manufacturing of wind turbine blades using thermoplastic composite matrix. An example of a thermoplastic material, which can be used in the production of wind turbine blades, is called PA-6 (this material is currently being researched by Delft University). Thermoplastic materials have a higher resistance to abrasion and fatigue (higher toughness) than most thermoset materials.[10] Their manufacturing process is also must faster (up to 6x). This is because they do not undergo the irreversible curing (cross-linking) process of thermoset materials. Because of this material is its ability to be melted and remolded, allowing complete reuse of material. The materials are also lower in cost[10] (see Table 1.0). There are however some drawbacks to using thermoplastic composites. Thermoplastic composites display a reduction of tensile strength when compared to thermoset materials a glass/epoxy thermoset composite has a tensile strength of 1166 Mpa, where a PA6-thermoplastic composite only has a tensile strength of 869 Mpa.[10] They also require a much higher processing temperature, which in turn means more energy, and as a result an increase in cost can be expected. Like any other new technology a large amount of economic investment is needed to research and industrialize this process for the use of wind turbine blades.
Material | Cost (∈/Kg) |
---|---|
Epoxy/Glass | 3.45 |
PA-6/Glass | 3.18 |
A new family of liquid thermoplastics (LTP) that are transformed via reactive closed-mold processes such as room-temperature infusion and flex-molding as used with composite thermosets have been recently introduced.[11] These novel resins based on a high-molecular-weight acrylic polymer cost less to manufacture than other thermoplastic composite technologies. The LTP, named as Elium,[11] has been brought to the level of epoxies with respect to mechanical properties, but with much higher toughness than epoxies and no need for post-curing to reach the glass transition temperature (Tg). Traditional thermoset processing equipment can be utilized in the reprocessing of wind turbine blades. Because of their thermoplastic properties, they are considered as thermoplastic resin for the wind turbine blades that are easily thermoformed and recyclable with even higher fatigue properties than epoxy parts.[12] Unlike unsaturated polyesters, Elium resins do not contain styrene.
Vacuum Infusion Processing[edit | edit source]
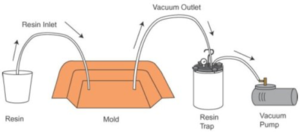
Thermoplastic polymers such as PA-6 can be manufactured using a vacuum infusion process (VIP).[10] The process of vacuum infusion follows as such (see Figure 5.0)
- There is a manual layup of dry fibers in a mold
- The dry fibers are heated to a temperature of 160°C
- The resin (which consists of monomers, initiators and activators) are mixed
- The resin is infused into the mold, the driving force is the pressure gradient created by the vacuum (20 min)
- The excess resin is sucked into the vacuum line and separated by a trap
- The resin solidifies (45 min)
This process results in minimal excess resin. Since the resin on it's own, is quite brittle an excess of it can induce an increased tendency to failure. Compared to its manual processing counter parts, VIP is able to lower weight, increase strength and maximize the fiber to resin ratio.
Current and Future Life Cycles[edit | edit source]
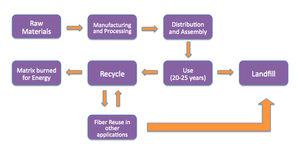
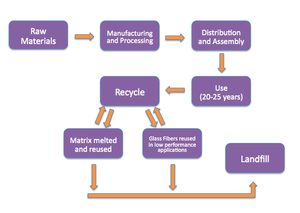
With the increase in popularity of wind farms, it is predicted that within the next twenty-five years 225,000 tonnes of rotor blade material will need to be recycled world-wide.[4] Currently wind turbine blades follow the life cycle as displayed by Figure 6.0, currently with landfill being the most popular option. During the 20-25 year lifespan of these blades it is imperative that recycling methods become optimized. In order to optimize these recycling processes a market/demand needs to be established for the recyclate fiber material in order to generate funds and encouragement.
With the use and multiple reuse of thermoplastic materials, and recycling of the fibers in low performance application the life span of the materials can be increased greatly (see Figure 7.0) and the amount of material disposed in landfills can be dramatically decreased. Carbon fibers should also be considered in the future design of rotor blades, because although they display and increase in cost they provide better mechanical properties and are more resilient in the recycling process than glass fibers.With this reduction in waste, the wind turbine will be an even more sustainable form of energy.
References[edit | edit source]
- ↑ 1.0 1.1 Wind Web Tutorial. Retrieved November 11, 2009, from American Wind Energy Association
- ↑ US and China in race to the top of the global wind industry. (2009, February 2). Retrieced November 11, 2009, from Global Wind Energy Council: http://www.gwec.net/index.php?id=30&
- ↑ Wolfe Island Wind Project. (June 26, 2009). Retrieved November 10, 2009, from Ontario Power Authority.
- ↑ 4.0 4.1 4.2 4.3 4.4 4.5 4.6 Larsen, Kari (2009, January/February). Recycling wind turbine blades. Renewable Energy Focus, 71-73.
- ↑ 5.0 5.1 5.2 5.3 5.4 5.5 Brøndsted P, Aage Lystrup, Lilholt H. Composite Materials For Wind Power Turbine Blades. Annu. Rev. Mater.Res. (2005) 35:505-538
- ↑ Putting it together – the science and technology of composite materials. Retrieved November 11, 2009,from NOVA: Science in the news
- ↑ 7.0 7.1 7.2 7.3 Pickering S.J. Recycling technologies for thermoset composite materials – current status. Composites: Part A 37 (2006) 1206-1215
- ↑ 8.0 8.1 8.2 8.3 Pickering S.J. Recycling technologies for thermoset composite materials – current status. Composites: Part A 37 (2006) 1206-1215
- ↑ 9.0 9.1 ReFiber ApS. Retrieved (2009, November 23): http://www.refiber.com
- ↑ 10.0 10.1 10.2 10.3 Van Rikswijk K., Joncas S., Bersee H. E. N., Bergsma O. K., Beukers, 2005 "Sustainable Vacuum-Infused Thermoplastic Composites for MQ-Size Wind Turbine Blades- Preliminary Design and Manufacturing Issues"
- ↑ 11.0 11.1 http://www.arkema.com/en/
- ↑ http://sites.google.com/site/hyucomposites