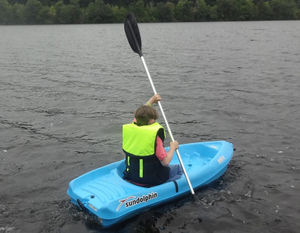
Fab labs, which offer small-scale distributed digital fabrication, are forming a Green Fab Lab Network, which embraces concepts of an open source symbiotic economy and circular economy patterns. With the use of industrial 3D printers capable of fused particle fabrication/ fused granular fabrication (FPF/FGF) printing directly from waste plastic streams, green fab labs could act as defacto recycling centers for converting waste plastics into valuable products for their communities. Clear financial drivers for this process have not been studied in the past. Thus, in this study the Gigabot X, an open source industrial 3D printer, which has been shown to be amenable to a wide array of recyclables for FPF/FGF 3D printing, is used to evaluate this economic potential. An economic life cycle analysis of the technology is completed comprised of three cases studies using FPF for large sporting equipment products. Sensitivities are run on the electricity costs for operation, materials costs from various feed stocks and the capacity factors of the 3D printers. The results showed that FPF/FGF 3D printing is capable of energy efficient production of a wide range of large high-value sporting goods products. In all cases, a substantial economic savings was observed when comparing the materials and energy related costs to commercial goods (even for customized goods). Using locally-sourced shredded plastic represented not only the best environmental option, but also the most economic. For the case study products analyzed even the lowest capacity factor (starting only one print per week) represented a profit when comparing to high-end value products. For some products the profit potential and return on investment was substantial (e.g. over 1000%) for high capacity use of a Gigabot X. The results clearly show that open source industrial FPF/FGF 3D printers have significant economic potential when used as a distributed recycling/manufacturing system using recyclable feed stocks in the green fab lab context.
- Kayak paddles
- https://re3d.org/
- All source files for Gigabot X
- re3D on SketchFab
Keywords[edit | edit source]
Circular economy; Distributed recycling; Energy conservation; Polymer recycling; Sustainable development; distributed manufacturing; life cycle analysis; recycling; recyclebot; 3-D printing; Open source hardware; Open hardware; RepRap; Recycling; Polymers; Plastic; Recyclebot; Waste plastic; Composites; Polymer composites; Extruder; Upcycle; Materials science;additive manufacturing; distributed manufacturing; open-source; waste plastic; extruder; upcycle
See also[edit source]
RepRapable Recyclebot and the Wild West of Recycling[edit source]
Recycling Technology[edit source]
- Recyclebot
- RepRapable Recyclebot: Open source 3-D printable extruder for converting plastic to 3-D printing filament
- Open Source 3-D Filament Diameter Sensor for Recycling, Winding and Additive Manufacturing Machines
- Improving recyclebot concepts
- 3-D Printable Polymer Pelletizer Chopper for Fused Granular Fabrication-Based Additive Manufacturing
- Mechanical Properties of Direct Waste Printing of Polylactic Acid with Universal Pellets Extruder: Comparison to Fused Filament Fabrication on Open-Source Desktop Three-Dimensional Printers
- Fused Particle Fabrication 3-D Printing: Recycled Materials' Optimization and Mechanical Properties
- Multi-material distributed recycling via material extrusion: recycled high density polyethylene and poly (ethylene terephthalate) mixture
- Mechanical Properties and Applications of Recycled Polycarbonate Particle Material Extrusion-Based Additive Manufacturing
- Wood Furniture Waste-Based Recycled 3-D Printing Filament
- Solar powered distributed customized manufacturing
- Mechanical Properties of Ultraviolet-Assisted Paste Extrusion and Postextrusion Ultraviolet-Curing of Three-Dimensional Printed Biocomposites
- Open Source Waste Plastic Granulator
- Open-Source Grinding Machine for Compression Screw Manufacturing
- Sustainability and Feasibility Assessment of Distributed E-Waste Recycling using Additive Manufacturing in a Bi-Continental Context
- Finding Ideal Parameters for Recycled Material Fused Particle Fabrication-Based 3D Printing Using an Open Source Software Implementation of Particle Swarm Optimization
- Waste Plastic Direct Extrusion Hangprinter
- Hangprinter for Large Scale Additive Manufacturing using Fused Particle Fabrication with Recycled Plastic and Continuous Feeding
Distributed Recycling LCA[edit source]
- Tightening the loop on the circular economy: Coupled distributed recycling and manufacturing with recyclebot and RepRap 3-D printing
- Technical pathways for distributed recycling of polymer composites for distributed manufacturing: Windshield wiper blades
- Plastic recycling in additive manufacturing: A systematic literature review and opportunities for the circular economy
- Energy Payback Time of a Solar Photovoltaic Powered Waste Plastic Recyclebot System
- Life cycle analysis of distributed recycling of post-consumer high density polyethylene for 3-D printing filament
- Evaluation of Potential Fair Trade Standards for an Ethical 3-D Printing Filament
- Life cycle analysis of distributed polymer recycling
- Distributed recycling of post-consumer plastic waste in rural areas
- Ethical Filament Foundation
- Green Fab Lab Applications of Large-Area Waste Polymer-based Additive Manufacturing
- Systems Analysis for PET and Olefin Polymers in a Circular Economy
- Potential of distributed recycling from hybrid manufacturing of 3-D printing and injection molding of stamp sand and acrylonitrile styrene acrylate waste composite
- Towards Distributed Recycling with Additive Manufacturing of PET Flake Feedstocks
Literature Reviews[edit source]
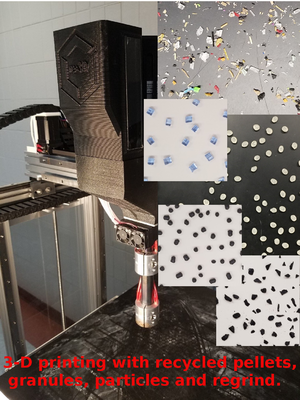
- Waste plastic extruder: literature review
- Life cycle analysis of polymer recycling literature review
- Solar powered recyclebot literature review
- Waste plastic extruder: literature review
- Life cycle analysis of polymer recycling literature review
Externals[edit source]
- Economist article on U. of Washington's HDPE boat, Oprn3dp.me
- https://ultimaker.com/en/resources/52444-ocean-plastic-community-project
- Another possible solution - reusable containers [1]
- Commercial https://dyzedesign.com/pulsar-pellet-extruder/
- ---
- Cruz, F., Lanza, S., Boudaoud, H., Hoppe, S., & Camargo, M. Polymer Recycling and Additive Manufacturing in an Open Source context: Optimization of processes and methods. [2]
- Investigating Material Degradation through the Recycling of PLA in Additively Manufactured Parts
- Mohammed, M.I., Das, A., Gomez-Kervin, E., Wilson, D. and Gibson, I., EcoPrinting: Investigating the use of 100% recycled Acrylonitrile Butadiene Styrene (ABS) for Additive Manufacturing.
- Kariz, M., Sernek, M., Obućina, M. and Kuzman, M.K., 2017. Effect of wood content in FDM filament on properties of 3D printed parts. Materials Today Communications. [3]
- Kaynak, B., Spoerk, M., Shirole, A., Ziegler, W. and Sapkota, J., 2018. Polypropylene/Cellulose Composites for Material Extrusion Additive Manufacturing. Macromolecular Materials and Engineering, p.1800037. [4]
- O. Martikka et al., "Mechanical Properties of 3D-Printed Wood-Plastic Composites", Key Engineering Materials, Vol. 777, pp. 499-507, 2018 [5]
- Yang, T.C., 2018. Effect of Extrusion Temperature on the Physico-Mechanical Properties of Unidirectional Wood Fiber-Reinforced Polylactic Acid Composite (WFRPC) Components Using Fused Deposition Modeling. Polymers, 10(9), p.976. [6]
- Romani, A., Rognoli, V., & Levi, M. (2021). Design, Materials, and Extrusion-Based Additive Manufacturing in Circular Economy Contexts: From Waste to New Products. Sustainability, 13(13), 7269. https://www.mdpi.com/2071-1050/13/13/7269/pdf