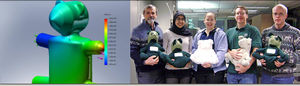
Start-Up Story[edit | edit source]
The Sustain-A-Bear project is the result of a combined effort of students and faculty members at Rensselaer Polytechnic Institute. Founded in 1824, Rensselaer Polytechnic Institute is the nation’s oldest technological research university. For many years the students of RPI have garnered numerous accolades and honors for their work on sustainability, including the Sustain-A-Bear project. The Sustain-A-Bear team of scholars consists of mechanical engineering doctoral students Christina Laskowski and Todd Snelson, and mechanical engineering senior Saadia Safir. Working under the guidance of Associate Professor Daniel Walczyk and Professor Michael Jensen from Rensselaer’s Department of Mechanical, Aerospace, and Nuclear Engineering, the team originally drafted this concept as a class project not knowing it would go on to inspire further innovations on sustainability. “We tried to pick an idea that would have a big impact,” Laskowski said. “The teddy bear market is huge, and despite all the billions of dollars of sales every year, no one has really looked into manufacturing stuffed animals in a sustainable way. That’s where the idea for Sustain-a-Bear was born.” At the 2009 ASME Manufacturing Science and Engineering Conference the Sustain-a-Bear team won first place in the Manufacturing Student Design Competition. [1]
Evolution of the Idea[edit | edit source]
While the original prototype, “Alpha,” was a one-color and hand-sewn stuffed bear made up of nineteen individual parts, the Sustain-A-Bear has since evolved in nearly every component. Now being offered in a variety of colors and patterns, the “Epsilon” version of this concept includes seven distinct and ultrasonically welded parts. The finished product is durable, machine washable, fully recyclable, and consists of PET plastic materials allowing it to melt rather than burn when exposed to fire. While the Epsilon Bear is certainly a refined version from the prototype, the students plan on continue to revise their methods and production for the Sustain-A-Bear. [1]
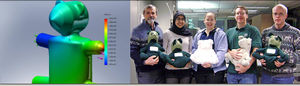
Construction of the Bear[edit | edit source]
For the Sustain-A-Bear project, this team of engineers and forward thinkers from Rensselaer Polytechnic Institute starts out with a strong base by using inexpensive and recyclable materials. Instead of thread and glue, the team utilizes ultrasonic welding technology to bond the seven pieces of fabric that would in turn become the Sustain-A-Bear. The pieces of fabric are assembled by using heat, pressure, and vibrations allowing for the bear to be entirely made from the same product. The inner stuffing of the bear is the same fleece material that can be found on the outside of the bear itself. This fleece is composed of the same material that accounts for a large amount of landfill currently. PET Plastic, properly termed polyethylene terephthalate, can be formed into a variety of textile products ranging from synthetic fibers to plastic bottles and for this team of engineers at Rensselaer, PET Plastic has in turn become a source of inspiration and innovation. With a fully recyclable end product as well, this teddy bear is both saving products from the landfill with its production, and at the same time allowing for a fully recyclable teddy bear that at the end of its life can be manufactured into another Sustain-A-Bear or other PET plastic products. [2]
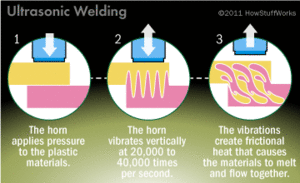
Methods of Production[edit | edit source]
While being composed of recyclable materials, the Sustain-A-Bear also employs sustainable methods of production. The ultrasonic welding, as mentioned previously, incorporates a high frequency vibration to combine heat and pressure in order to bond the fabric pieces together. By using ultrasonic welding the production cuts down on time as well as money and space. [3] All together, the production of these stuffed bears requires very little water and a small work space and also uses 90% less energy than the going rate for a stuffed animal of the same size. [1]
Notes and references[edit | edit source]
Green@Rensselaer [1] Green Upgrader [2] How Stuff Works: Ultrasonic Welding [3]