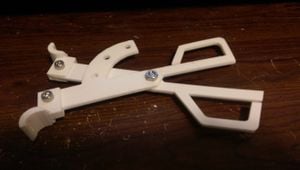
Complex Surgical Retractor[edit | edit source]
Project developed by Tyler Jubenville
Abstract[edit | edit source]
This design seeks to address the high cost and many variations of complex surgical retractors used today. This design is intended to serve as a potential cheaper replacement for surgeons today, or in locations where sterilization techniques and equipment are not ideal.
Bill of Materials[edit | edit source]
Quantity | Material | Source | Cost ($) | Total ($) |
---|---|---|---|---|
38 g | PLA | Hatchbox - Amazon | $23/kg | $0.874 |
1 | screw m6 x 12mm | Hardware Store | $0.89 | $0.89 |
3 | screw m5 x 16mm | Hardware Store | $0.75 | $2.25 |
3 | 5mm bolt | Hardware Store | $0.30 | $0.90 |
1 | 6mm bolt | Hardware Store | $0.34 | $0.34 |
Total Cost | $5.254 |
STL and Openscad files available at Thingiverse
Tools needed[edit | edit source]
- MOST Delta RepRap or similar RepRap 3-D printer
- 5 mm and 6 mm Allen Wrenches
Skills and knowledge needed[edit | edit source]
This project is simple to assemble and no special skills are required.
Technical Specifications and Assembly Instructions[edit | edit source]
- Be sure to print with support material turned on, to ensure the modular tip components print.
- Print (About 3 hour print time, with 0.1 mm Layer height, 50% fill density)
- Place one side of the retractor on top of the other and insert 6mm screw through the hole closest to handle. Attach bolt.
- Clean out the modular tips and press fit onto the base. Insert 5mm screw and secure with bolt.
- Use remaining 5mm screw and bolt to lock in position using the slide lock, if desired.
Cost Comparison[edit | edit source]
Due to the complex financial systems involved in the medical industry, as well as comparing a disposable part with a reusable part, this estimation will vary a great deal, depending on the circumstances of the hospital and healthcare system. In addition, the standard part will be reprocessed multiple times to ensure sterility. It has been shown that it is possible to 3D print components in a sterile environment and ensure they are sterile.[1] In addition, it will be assumed that the personnel costs for running an autoclave and a 3d-printer will be roughly equivalent.
Commercial Equivalent[edit | edit source]
As mentioned above, the cost of a commercial equivalent will vary depending on the purchasing practices of a hospital, but some equivalent devices can be found for around $100-$150.[2] In addition, the reprocessing requires use of an autoclave, which vary in price based on capacity. $2000 will be used as the initial cost of the autoclave in these calculations.
Device Cost[edit | edit source]
As shown above, the cost of the device is around $5.25. The cost of the printer used to produce it is about $500.
Cost Savings[edit | edit source]
Per unit basis: $94.75, 94.75%
- Stainless steel retractor must be used in about 20 surgeries to be more viable
Inital investment included: $1594.75, ~76%
- Stainless steel retractor must be used in about 304 surgeries to be more viable
Note: This device is not fda approved or certified and thus would likely see some sort of price increase.