Introduction
Lighting is taken for granted in industrial countries and in many urban areas of developing countries. It is hard for many people to imagine living at night without being able to obtain light at the flick of a switch. However, about half of humanity, over 2500 million people, live without much light after sunset, since they do not have access to grid-connected electricity.
Lighting in the rural areas of developing countries is generally provided by candles or kerosene lamps, while torches (or flash-lights) powered by expensive, throw-away dry-cells are used as a portable source of light for intermittent use.
What is light?
Light is electromagnetic radiation; the human eye is sensitive to a spectrum with visible colours as seen in a rainbow. When these colours are mixed they appear as white light. More energy is present in the light of the upper or violet/blue end of the spectrum than at the red end. Therefore, more energy is generally necessary to produce the blue-violet component needed to produce what to the eye appears as white light. Therefore the quality of light (in colour terms) influences the energy requirement; if colour does not matter then it is at least theoretically more efficient to use a red or orange light, and this in fact is common practice in the case of street lighting where the most energy-efficient lights are used, namely orange/yellow sodium lights. Clearly, for domestic purposes there is merit in paying something extra to achieve a white, or near-white light.
Light intensity, or illuminating power of a light source in any one direction is commonly defined in candela, which although it has a rigorous scientific definition, for practical purposes can be thought of as 'candle-power'; i.e. the output from a standard paraffin-wax candle. The rate at which light is emitted is measured in lumens, which are defined as the rate of flow of light from a light source of one candela through a solid angle of one steradian. A more easily understood approximation of this would be to imagine a one candela candle at the apex of a conical lampshade with its sides sloping at about 70 degrees to each other; the conical beam emitted, diverging at about 70 degrees, would be about one lumen.
Methods of providing light
There are two main physical principles by which light may be produced:
- incandescent
- fluorescent
The incandescent principle depends on heating a source to a temperature in the region of 2000, 4000 or 6000°C to obtain reddish, yellowish or white light, respectively. Typical examples are candles and lamps utilising a bright flame (where white hot or incandescent particles of carbon in the flame produce the light) and incandescent filament light bulbs where a fine coil of tungsten wire is heated (in a vacuum or inert low pressure gas to prevent the filament oxidising or burning) by an electric current passing through it. All incandescent light sources, whether flames or electrically heated filaments, tend to produce more heat than light and are therefore relatively inefficient in the rate of conversion of energy to light.
Fluorescence occurs under certain conditions when a material can be made to glow with a 'cold light'. Fluorescence is a phenomenon in which the atoms of a gas, vapour or solid are excited in such a way that they emit light. In some cases such as sodium and mercury vapour discharge lamps (used commonly for street lighting) vapour in a glass tube emits the light. In other cases such as the commonly used fluorescent tube lights, ultraviolet light, which is invisible to the eye, is emitted by exciting mercury vapour atoms within the tube, and this in turn causes a white translucent coating in the tube to fluoresce with a whitish light.
In other words, the coating converts invisible ultraviolet light into visible white (or near-white) light. Most fluorescent processes involve some expenditure of electrical energy, so they are accompanied by the production of some heat. (Non-electrical fluorescence is used where the mantles of pressure lamps and gas lamps are heated and emit a much brighter and whiter light than would occur simply as a result of their temperature.)
For practical purposes, the options for lighting reduce generally either to lamps that run on fuels, or electric lights. Table 1 indicates the options and their relative lighting capability.
Type of light | Energy source | Intensity (lumens) | Efficiency (lumen/W) |
---|---|---|---|
Candle | Paraffin wax | 1 | .01 |
Oil lamp (wick) | Kerosene | 1-10 | .01-.1 |
Hurricane lamp (wick) | Kerosene | 10-100 | .1-.2 |
Oil lamp (mantle) | Kerosene | 1000 | 1 |
Gas lamp (mantle) | 1 .p.g (eg butane) | 1000 | 1 |
Filament lamp 3W | Electricity | 10 | 3 |
Filament lamp 40W | Electricity | 400 | 10 |
Filament lamp 100W | Electricity | 1300 | 13 |
Fluorescent 15W | Electricity | 600 | 40 |
Fluorescent 30W | Electricity | 1500 | 50 |
Mercury 80W | Electricity | 3200 | 40 |
Sodium sox 35W | Electricity | 4500 | 128 |
More important to the user than the efficiency in lumen/watt is the cost per lumen. Kerosene and candle wax are cheaper sources of watts than any form of electricity, and this partially makes up for their inefficiency, but not for their poor quality light (wicks) or the amount of heat. Kerosene lamps produce better light, but they are unpleasantly noisy and uncomfortably hot to be near in a tropical climate; they also use much more fuel than wick lamps, and are troublesome to start. Cylinder gas lights provide a slightly more expensive but convenient alternative.
All combustion lamps pose a real fire risk. Kerosene and butane are also becoming increasingly expensive and are sometimes in short supply in developing countries. Therefore the rest of the technical brief addresses the use of electric lighting in rural 'off-grid' locations.
Electrical energy storage for lighting in rural areas
Since electric light is normally needed on demand, the only way of ensuring this is to provide electrical storage in the form of a battery. It is possible to use primary batteries (ie dry cells) which are charged when bought and thrown away when exhausted. These are convenient but extremely expensive in terms of electrical energy costs and are particularly expensive in the tropics since transport and distribution costs are incurred in moving them to the rural areas.
Secondary batteries, which are rechargeable, are more cost-effective than primary batteries, but an investment in equipment to recharge them becomes necessary. The two main secondary battery options available are lead-acid and nickel-cadmium batteries; the former being similar to the batteries used in cars. Nickel-cadmium batteries are generally less available (except as dry-cell substitutes) and cost more, but they can be more robust and tolerant of abuse than lead-acid batteries. However they self-discharge quite quickly if not used. Electrical energy from a lead-acid battery can cost as little as one twentieth to one fifth as much for the same amount of energy delivered from primary (dry) batteries.
For most lighting purposes lead-acid batteries are probably the easiest and cheapest secondary cell option. They are available as deep-discharge batteries which have a longer life than car batteries, and if looked after tend to be better for general electrical storage. Most lead-acid and nickel-cadmium batteries require regular checking of their electrolyte level and topping up with distilled or deionised water, (not with acid). Rain water can be used for this purpose, providing it has not been contaminated in any way. Low maintenance and maintenance-free lead-acid batteries are also available, at slightly increased cost.
An important point to note with lead-acid batteries is that their life is considerably shortened if they are over-discharged. Ideally they should only be discharged to about 50% of their full rating; ie a 60Ah (ampere-hour) battery should only be discharged to 30Ah before recharging it.
Typical present deep-discharge load-acid battery costs are in the region of £60/kWh of total rated capacity or £120/kWh of usable storage, while nickel-cadmium will be about three times this level. The cost increases with some specialist types and very small batteries.
Batteries are generally provided with nominal voltages in multiples of 2V; common larger capacity lead-acid batteries will be 12V or 24V nominal voltage. Filament bulbs can be obtained which operate at almost any battery voltage, but fluorescent and vapour discharge lamps need 'mains voltage' (typically 240V) ac (alternating current). This can be readily provided by interfacing an appropriate inverter between the battery and the lamp; the high efficiency of such lamps make it well worth investing in an inverter if long hours of light are needed. Some small fluorescent lights in fact include a built-in inverter, and these often run at higher frequency than mains frequency which improves the light's efficiency still further. In most cases it will be best to obtain a fluorescent light with a built-in inverter so it can be directly connected to a 12V or 24V dc (battery) source.
Finally, it is important to note that cable runs should be kept as short as possible with low voltage supplies, (or very heavy cable must be used) otherwise significant losses will occur in the cables. A 1.2V voltage drop in a 12V system represents a loss of 10% of the power transmitted down the cable. The voltage drop is numerically equal to the current in amps times the resistance of the cable in ohms; 1mm² copper cable will have a voltage drop of 0.025A, so 10m of 1mm² cable carrying 1.25A will have a voltage drop of 1.25 x 0.042 x 10 = 0.525V. This represents about 96% cable efficiency, which is acceptable. However, 100m of the same cable will cause a voltage drop of 5.25V which will cause the light not to work and in any case represents a quite unacceptable loss of nearly 50% of the energy supplied.
A 30W fluorescent light (for example) running off a battery with an inverter for six hours per night will consume 180Wh each 24 hours. Losses in the inverter, cables and the battery will increase this requirement to about 300Wh/24h. To avoid more than 50% discharge and provide a nominal 24 hours storage capacity would require, with the above example, a battery with a usable capacity of 600Wh (1200Wh to total discharge), costing in the region of £80.
Power sources for charging batteries
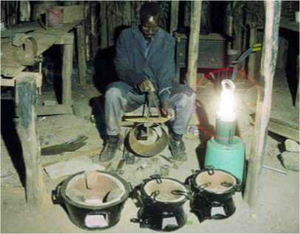
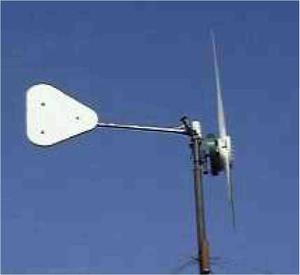
There are four main methods by which the electricity for charging may be provided:
- taking the battery to the nearest mains supply and putting it on charge
- using a small engine-powered generating set
- using a photovoltaic charging system (solar cells) - Figures 1
- using a small wind generator - Figure 2
Using a generating set imposes considerable problems as, unless power is being generated for other purposes too, the charging current, which is acceptable for small battery storage for just one or two lights is rather low for even the smallest generating sets; hence the engine needs to be run at part load which results in inefficient fuel use and is bad for the engine.
A photovoltaic system is by far the most universally applicable, as adequate sun for charging can be found in most parts of the world, and such a system, apart from occasional cleaning of the array, requires almost zero attention. The snag is that photovoltaic arrays currently cost (delivered and installed) in the region of £3-5/Wp (peak Watt). The supplier should be able to advise on the size needed (and can generally supply a battery and lighting system too). To run a 30W light for six hours would typically require, in a sunny tropical location, two nominal 40W solar modules, and would therefore cost in the region of £400. Areas with extended cloudy periods may need up to twice this capacity.
The last option is to use a small wind generator; this will generally be a cheaper option than solar power in locations having mean windspeeds greater than 4.0m/s in the least windy months. A separate technical brief gives further information on wind generators and gives a rule of thumb that the required rotor area of the wind generator for small-scale applications like lighting will be:
Energy demand (kWh/day)
Rotor area (m2) = -----------------------
0.0048 v3
where v is the mean windspeed in the least windy month of the year. For the 30W lamp for six hours example, it follows that a 0.5m² rotor wind generator will suffice at 5m/s, a 1m² rotor is needed at 4m/s and a 2.3m³ rotor at 3m/s. The typical cost of wind generators is around £400-600/m² for small machines (installed).
Conclusions
In our example of a 30W fluorescent light, which is comparable in illuminating power to a 100W tungsten filament lamp and brighter than a pressure kerosene lantern with a mantle, we can conclude that to operate it in a rural 'off-grid' location using wind or solar power, we will need the following items:
Item | |
12V 30W fluorescent light with built-in inverter unit | |
10m cable, connectors, etc | |
1200Wh battery (rated) giving 6000Wh usable capacity | |
plus either: | |
60-90W (rated) solar array with battery charge regulator (depending on solar irradiation)
or 0.5 to 2m2 rotor area wind generator with battery charge regulator |
|
This may sound a lot to pay for a single light, but the running costs will be negligible and good quality light will be reliably available. A pressure lantern, which is much less satisfactory, would cost only about £15-30, but it would consume in the region of 5 litres of kerosene per week on the same duty cycle which would cost typically £75-150 per year. The price of solar panels and small wind generators is declining in real terms as production increases, while the price of kerosene will continue to rise. There are tens of thousands of small photovoltaic lighting systems in use in developing countries (eg 4000 in use in Mongolia in 1990) and tens of thousands of wind-powered lighting systems particularly in China.
Further information
Publications
Kerosene & Liquid Petroleum Gas (LPG) Technical Information Service Practical Action Technical Brief
Solar Photovoltaic Products: A Guide for Development Workers Anthony Derrick, Cathrine Francis & Varis Bokaldis ITDG Publishing, 1989
Rural Lighting: A Guide for Development Workers, Jean-Paul Louineau, Modibo Dicko, Peter Fraenkel, Roy Barlow & Varis Bokalders, ITDG Publishing, 1994
Useful contacts
Winrock International India (WII)
http://www.winrockindia.org
Winrock International (WI)
http://www.winrock.org
Winrock has developed a solar lantern for the
Indian sub continent
Intermediate Technology Consultants
solar lantern web site
http://itcltd.com/glowstar/
Sollatek
http://www.sollatek.com/
Equipment suppliers
Chris Crotty (For Al P Anton)
Kyocera America Limited
8611 Balboa Ave
San Diego CA 92123 - 1580
USA
Tel: + 1 619 576 2600
Fax: + 1 619 569 9412
Manufacture of solar lanterns
Pennmaritime Solar
Baxter House
48 Church Road
Chavey Doen
Ascot, SL5 8RR
United Kingdom
Tel:+44 (0)1344 891118
A UK supplier of the Siemens Solar Lantern