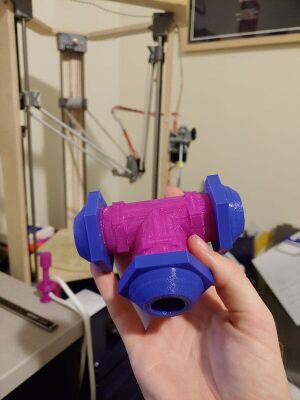
Accessing clean water is still a struggle for many people throughout the world. In areas devastated by natural disasters, it can take years for the infrastructure to be rebuilt. Makeshift water piping has been a massive undertaking in Nepal especially where an earthquake devastated the area a year ago. Organizations such as Field Ready are hard at work making sure water supply systems in the area are sanitary and helpful for those who need it. The T-fitting module was specifically requested by Field Ready to join hoses in the field to allow for more pipes to be ran while the entire system staying sanitary. The request Source can be found here.
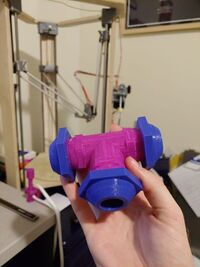
Bill of Materials[edit | edit source]
- PLA Filament was used for printing all components. Components should be printable in other materials as well.
- All CAD models (STLs and SCAD) can be found on Youmagine.
- One T Fitting (Printed Component)
- Cost: $1.12 for 56g of PLA Filament at $20/kg
- Three Hose Caps (Printed Component)
- Cost: $0.34 for 17g of PLA FIlament at $20/kg each
- O-Ring and Washer
- Already equipped with manufacturing O-rings for hoses as indicated here.
- Equivalent Market Cost $1.48 for 6 of each
- Link to STLs and SCAD Files
Tools needed[edit | edit source]
- MOST Delta RepRap or similar RepRap 3-D printer
- Sharp knife to remove excess filament from threads
Skills and knowledge needed[edit | edit source]
- Knowledge of operating a 3D printer is required for manufacturing components.
Technical Specifications and Assembly Instructions[edit | edit source]
Print Instructions[edit | edit source]
Material: PLA
Layer Height: 0.3mm
Shell Thickness: 2mm
Fill Density: 25%
Print Speed: 50 mm/s
Printing Temperature: 210 C
- Print time estimate: 5 hours
- T Fitting: 2.5 hours
- Hose Cap: 50 minutess each
Assembly Instructions[edit | edit source]
- 3-D print all components
- Support material should be disabled to reduce waste plastic. The design prints fine without but using support may improve quality of parts.
- Insert O-ring and Crush Washer into T Fitting
- Slide Hose Cap over hose and feed hose into T fitting
- Tighten Threads on hose cap to crush washer into O ring and create seal
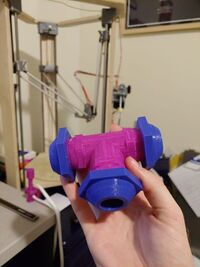
Common Problems and Solutions[edit | edit source]
- Make sure retraction is enabled when printing components. If parts have extra plastic in threaded regions, assembly becomes difficult.
- Complete seating of hose in T fitting is important to ensure a good seal.
Cost savings[edit | edit source]
- One T Fitting Cost: $1.12 for 56g of PLA Filament at $20/kg
- Three Hose Caps Cost: $0.34 for 17g of PLA FIlament at $20/kg each
- O-Ring and Washer Cost: $1.48 for 6 of each
- Total Cost: $2.20
- Equivalent Commercial Product: $8.78
- Cost Savings: $6.58 (Reduction of 74.943%)
Benefited Internet Communities[edit | edit source]
- Communities that would benefit from device