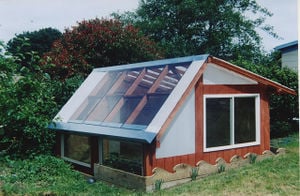
Welcome to our straw bale greenhouse. The following page will take you with us on our greenhouse building adventure. We will discuss the process, what worked best and did not work, problems we had, how much time it took to build, and the money spent on the project. Over all we hope that this is a fun and comprehensive look at what we did to make this project come together. The reason that we chose to build a straw bales greenhouse is that both Scott (my building partner) and I would like to get into alternative building as a career and we thought that this would be a good place to start and learn from.
Our plan is to build a straw bale greenhouse where Kiva can grow chili peppers, tomatoes, and lots of other yummy warm weather plants. The reason we decided to build with straw bale was to gain experience with this material and the great insulative value of it. Scott and I decided to have two of the walls straw bale and the other two wood and glass. Where we live no permits are required for a 10' x 12' greenhouse, so we decided these would be the inside dimensions. To receive optimal year-round sun in our area the glass on the south facing wall is at a 40 degree angle. At the building site there is plenty of morning sun and not much evening sun so we opted to have our east side be glass and our west side be straw bale.
Building Process[edit | edit source]
Foundation[edit | edit source]
This is the yard before we did any work. The garden box and wheelbarrow are right where the greenhouse is going to be built. This part of the yard gets the most light throughout the day and putting the greenhouse here will not block the view from the house. The shade of the house next door will reach the greenhouse late enough in the evening that it will not have any significant affect.(Fig 1)
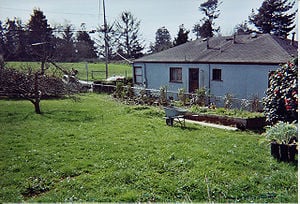
Because the yard is on a slant we had to level it to lay the foundation. On the side farthest away form the blue house we had to dig down about three feet. Moving all of the soil by hand took much longer then we originally thought and if I were to do it again I would consider renting a small bulldozer.(Fig 2) Once we leveled the ground it was time to dig out the area for the foundation. Scott is standing on the northern side and the fence is to the west. The northeast corner was the hardest corner to dig out and get the forms in place. It is all clay after the first foot and a half and was extremely difficult to work with. This corner took us almost the same amount of time to as the entire rest of it. When digging out where the foundation was to go it was really important to make sure it was level, square, and all four sides were even with each other so that our foundation would be level, flat, and square.(Fig 3) After the ground was dug and leveled, we put in the forms for the foundation, the posts for the retaining wall, and the rebar. The inside forms are 12ft by 9ft and the outside forms are roughly 14ft by 12ft. Because the north and west walls are going to be straw bale the foundation on those two sides has to be 18in wide. This is so that a bale can sit on its side and not hang over the edge of the foundation. We have three pieces of rebar running down each side of the foundation, which are sitting three inches off the ground and the poles for the retaining wall go into the ground about two feet and are leveled.(Fig 4) The concrete for the foundation we bought premixed and ready to pour. To get it from the wheelbarrow into the forms we used a small piece of metal stovepipe, which we got from the recycling center, that made a perfect chute. In total we used about two and a half yards of concrete. Everything went really smoothly, the forms held and we had no disasters. Once the pour was complete we pushed L shaped rebar pieces into the foundation on the North and West sides so that they were sticking up vertically. These are to help hold the bales in place.(Fig 5&6)
-
Fig 2
-
Fig 3
-
Fig 4
-
Fig 5
-
Fig 6
Framing[edit | edit source]
The framing starts to go up and the greenhouse is taking shape. We bolted pressure treated 2x4's to the top outside edge of the foundation and secured the rest of the frame to that. It is constructed like a traditional small building except we did not include any studs or other excess wood. The rafters are 2x4's instead of the standard 2x6's which helped to reduce the amount of wood used and by having straw instead of timber to infill our walls is reduced our 2x4 usage by 152 board feet. In order to slow the wicking process between the earth and the concrete we put French drain around the foundation.(Fig 7&8)
-
thumb
-
thumb
Windows[edit | edit source]
The first window we put in the greenhouse is the one on the east side.(Fig 9) This window lets in a lot of morning sun and helps take the night time chill off. All of the windows are second hand and recycled that we bought locally. A problem we had with the first window is that it is made to go vertical not horizontal, the way we installed it. Because of this there are springs in the window to help it go up and in this case, being on its side, the springs help it open but it is very hard to close. To fix this we removed the springs and now it slides easily in both directions. Another problem we discovered is that the drains for the window are now on the side instead of the bottom where they are supposed to be. This has lead to a leak right in the center of the window which could eventually lead to rot. On the south side we installed two long windows on the bottom. These will not let in much light but they will let in a little and are mostly for aesthetics.(Fig 10)
-
thumb
-
left
Roof[edit | edit source]
We stained the wood before putting the roof and glass on because we did not want to get stain on either of them. Stain also helps the sealant attach to the wood and forms a better bond. We considered using linseed oil to seal the wood but because it has to be continually reapplied we decided it would be inappropriate for the greenhouse. The property that the greenhouse is on is usually a rental and it would be hard to maintain while not living here. The stain we used is Behr deck plus and is water based. For the roof we used a plastic material that is shaped like cardboard and has an R-value of about 2.5 which is better than the non-insulative corrugated fiberglass roofs normally used on greenhouses. This material is also flat which makes it easy to install.(Fig 11) Putting up the glass turned out to be more difficult than expected. To hold it in place we hammered two wooden blocks below each sheet of glass. Then around the sides of each window, between the glass and the wood, we put double-sided foam tape as a sealant. Outside of that we were suppose to put a special kind of caulking but it turned out to be a disaster. It was very messy, got everywhere, did not make a proper seal, and was a pain to work with. What we should have done is had the rafters a little farther apart so that we could have a piece of wood in-between each piece of glass. This would allow us to screw another piece of wood on the top of the glass to help hold it down and add more protection from leaks.(Fig 12)
-
-
thumb
Siding[edit | edit source]
After the roof and glass were up we put on the roof cap and siding. Some of the siding was 4'x8' sheets of exterior plywood called T1-11 but we also used some of the roofing material on the east side to let more light in. Once the siding was up we stained that as well.(Fig 13)
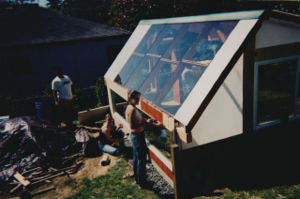
Bale walls[edit | edit source]
For the walls we used three string bales of rice straw. We figured we would need about 18 bales but got a couple extra for mistakes and to test stucco on. Before putting them into the greenhouse we stacked them on wooden pallets to keep them off the ground and dry. The first bale turned out to be our trouble bale because we did not have it over far enough to the west and it made an indentation in the wall. This spot will be discussed in more detail later on.(Fig 14) Once the first layer of bales was down we pushed vertical pieces of rebar through them that were tall enough to go six inches into the top bale. When putting the second layer on it was important to watch the rebar and make sure it stayed straight and did not bend. We had to cut one of the bales at an angle to fit into the rectangular section to the left of the door. First we tried to use a saw but this did not work very well and we do not recommend it. What we found to work best was a pair of long bladed garden sheers.(Fig 15) There were about seven bales that we had to shorten by using a baling needle. A baling needle is just a big version of a sowing needle. Ours was made out of an old copper-grounding rod. First we would restring the bale and tie them really tight by using a trucker's hitch before cutting the original strings off. To get the bales down tight over the rebar we put a two by four over the top of each bale and had someone hang on each side.(Fig 17) We found this to be the only way to get the top bales really tight. In the end we only ended up using the 18 bales that we predicted we would need. Here she is with all of the bales in her before we put any stucco on. How satisfying.(Fig 18&19) To help hold the walls in place we made top plates out of 2x4's that were put together like a ladder. We ran wire cables over these plates and secured them to the foundation. Every cable has a turn buckle on each side of the wall so they can be tightened down. Once they were secure we filled every crack between the bales with as much straw as could be stuffed into them.(Fig 20)
-
Fig 14
-
Fig 15
-
Fig 16
-
Fig 17
-
Fig 18
-
Fig 19
-
Fig 20
Plaster[edit | edit source]
The first layer of stucco is a clay slip. This is made of clay that has been put through a screen, soaked in water, and blended into a creamy texture. When we had 50 gallons made we rented a plaster sprayer to apply the mixture onto the walls. If we did not have this sprayer we would have had to apply it by hand which would have taken a long time and we could have never gotten it to penetrate the walls deep enough. The purpose of the clay slip is to create a surface to which the rest of the stucco can bind to.(Fig 21) To mix the second layer, which is called the scratch layer, we rented a cement mixer. This layer is a combination of sand, clay, and straw and is the consistence of brownie mix.(Fig 22) We applied the scratch layer to the bales after the slip had dried a little. This is a thin layer put on by hand into which we made horizontal lines with our fingers so that the next layer would sick to it. When applying the scratch layer it is best to start on the bottom of the wall and work your way up pushing the mixture in an upward direction.(Fig 23) The third layer or filler layer was mixed with our feet on top of tarps. This layer is made up of the same materials as the scratch layer but the proportions are a little different. There is less clay, less water, and the pieces of straw are longer.(Fig 24) As with the last layer it is important to work in an upward direction so that each piece of stucco is bonded with the one below it. We would mix up a small amount of filler and break it into small hand sized balls that we applied one at a time dampening the wall before sticking them on. There are a couple of reasons why it is important to dampen the layer underneath before adding new material on top. One is to help the new stuff stick and two so that the layer beneath it does not suck out the moisture from the one on top and cause cracking. With this layer you can take out all the impurities of the wall. If there is a little hole you just fill it, hence the name filler layer. The application of this layer was extremely time consuming and took approximately 120 hours by itself.(Fig 25&26) Once the filler layer was complete it was time to do any artwork that we wanted on the walls. The artwork is done with the same mix as the filler layer and is like working with clay in ceramics class. It is important to make your designs much bolder than you want your finished product to be so when you add the last coat of stucco the detail is not lost.(Fig 27&28) The preparation of the materials for the last coat took a long time. The last coat is made up of horse manure, clay, sand, and flour paste, all of which had to be processed. The sand was run through a 1/8 inch screen(Fig 28), the manure was pushed through a ¼ inch screen(Fig 29) and the clay needed to be blended into the same creamy consistency as the slip. Fortunately, we had some help with this process from a class at the local university. Once the materials were ready we mixed them like the last layer, on a tarp with our feet, and applied it to the wall by hand. This layer did not have the right ratios and had to be redone later due to cracking. The lesson we learned here is to make sure that your test strips are right and you have the proportions correct.(Fig 30&31) This is our test strip bale. In the future I will make all of my test strips about twice as big as what I did here so that I get a better feel of how it will look when it dries.(Fig 32) The mistake in our plaster turned out to be not enough sand or horse manure. Our final ratio was two parts sand and horse manure to one part clay and lots of water to make it go on easy with a trowel.(Fig 33)
-
Fig 21
-
Fig 22
-
Fig 23
-
Fig 24
-
Fig 25
-
Fig 26
-
Fig 27
-
Fig 28
-
Fig 29
-
Fig 30
-
Fig 31
-
Fig 32
-
Fig 33
Garden beds[edit | edit source]
The garden beds sit right on the ground with each side buried a couple of inches into the floor. They were put together inside the greenhouse and then leveled which was hard to do with them in there because they got in the way. If I were to do it again I would first dig the trenches for the beds to go into and level them off. After they were level I would then put the beds together in place.(Fig 34) Once the beds were built we filled them with soil that came from the garden box that used to be where the greenhouse is now. To fill them we brought the soil in one bucket at a time. This was a lot of work.(Fig 35)
-
Fig 34
-
Fig 35
-
Fig 36
Floor[edit | edit source]
Before we put the garden boxes in we compacted the floor with a hand tamper, which consists of a steel plate at the bottom of a stout pole, and shaped the floor so that it was at a slant ending at the hole in the foundation. Once the garden boxes were in place and full we laid gravel on the floor. Scott shoveled the gravel in through the window and then leveled it out making the floor flat. We decided to use gravel to keep the floor clean and retain some heat.(Fig 36)
Conclusion[edit | edit source]
The most important advice that we could offer anyone who is going to attempt this type of project is to plan, plan, plan. We cannot emphasize how much we would have benefited from a detailed design, plan of attack, and cost analysis. A large amount of money went to hidden costs due to our lack of planning. The other major problem we encountered was the application of the cob-filler layer. There has to be a better way to seal the straw bales that does not require so much work. Some of the successes we had include: the use of a truckers hitch when retying the customized bales, the cement mixer for mixing the plaster, a texturing gun for applying the slip layer, and finally the dual purpose wood for the foundation forms and the retaining wall. The most satisfying part of the project was how so many people became involved. People just walking by on the street stopped to ask us what we were doing and to complement our work. It provided a sense of community and built strong friendships. We are extremely happy with the outcome and Kiva has been able to grow tomatoes and peppers with ease for the last two years.
Time Table[edit | edit source]
All of our time is measured by how many hours it would take one person to complete a portion of the project. Mostly there were two people working at once and sometimes it was as many as forty, so we broke it down into the amount of time it would take one person to do the work by him or herself.
Task | Hours spent |
---|---|
Research | 24 hours probably a lot more here. |
Shopping | 30 hours |
Digging | 34 hours |
Building forms and preparing to pour | 21 hours |
Pouring concrete | 32 hours |
Building the frame | 68 hours |
Staining the wood | 27 hours |
Putting roof on | 20 hours |
Shaping floor | 6 hours |
Door frame | 5 hours |
Glass roof | 19 hours |
Windows | 20 hours |
Siding | 21 hours |
Bales | 32 hours |
Preparing bales | 18 hours |
Stuccoing | 303 hours |
Retaining wall | 6 hours |
Beds | 18 hours |
Fixing leak | 12 hours |
Misc | 36 hours |
Total hours worked: | 742 hours |
Money, Money, Money[edit | edit source]
This is all the money that was spent on the greenhouse. We kept it divided up so we could get an idea of where the most costly areas were. By doing this we can find ways to cut back expenses in the future.
Parts and Cost List[edit | edit source]
Item | Cost ($USD) |
---|---|
Wood | 670 |
Hardware | 314 |
Reciprocation Hammer Rental | 50 |
Lag bolts | 25 |
Windows | 240 |
Doors | 15 |
Concrete | 316 |
Tarps | 89 |
Barrel | 18 |
Pipe | 16 |
Stake puller | 4 |
Gravel | 33 |
Roofing | 345 |
Stain | 74 |
Sealant | 52 |
Straw Bales | 174 |
Siding | 122 |
Cement mixer rental | 32 |
Sand | 52 |
Clay | 10 |
Misc Rentals | 88 |
Total Cost | $2772 |
Updates[edit | edit source]
Problems within the first year[edit | edit source]
When the bottom first bale was put in it was not flush with the rest of the wall. This created an indentation in the wall that needed to be filled. The first thing we tried to do to fix this spot was to tie a 6 inch section of straw into that hole and then plastered over it. We found that un-baled straw can not be compacted enough for stucco to adhere. So we cut this entire part of the wall off to redo it.(Fig 37) We bought a piece of peg board and tied it onto this section. The reason for choosing peg board is that it is breathable and can be tied easily due of the holes in it. When we put the peg board on we in filled behind it with as much straw as could fit. In order to get the stucco to stick to the beg board we applied a thin layer of cooked flour, horse manure, and sand.(Fig 38) After the horse manure mixture dried the scratch coat and the filler layer went on easily. So far the peg board has worked well and this spot blends in with the rest of the wall.(Fig 39&40)
-
Fig 37
-
Fig 38
-
Fig 39
-
Fig 40
We had a small problem with the two windows on the bottom south side of the greenhouse. The glass in them come loose and slid down creating a gap between the glass and the top of the molding.(Fig 41) In removing the glass out we realized the entire window had been installed upside down and the rubber stoppers that were in the window to hold the glass up were on the top instead of the bottom. To fix this we made our own stoppers out of wood and put them in under the glass to hold it in place.(Fig 42)
-
Fig 41
-
Fig 42
When the rains come in the fall we realized that we had a huge problem. The southwest corner was leaking and the water was going right into the straw bale wall, which is the worst thing that can happen. Moisture is the enemy to straw bales and a wall will rot away if it is allowed to get wet. You can see in the picture where we noticed the water was coming through.(Fig 43) First we removed the siding and saw that there were two leaks. One on the top where water was getting in between the siding and the bale and the lower leak where we had not sealed the window all the way to the foundation.(Fig 44) We removed any wet straw that we could and left it open to dry out for a month or so.(Fig 45) While drying the entire greenhouse was covered in a tarp so that no rainwater could find its way to the exposed wall. We also made sure there was lots of air circulation around the open area.(Fig 46) To fix the leaks we sealed the window all the way down to the foundation and added a rain gutter onto the bottom of the glass. This gutter canals all the water that comes down the south side of the building so that it no longer runs down the front of the siding and the two lower windows. The late rains in spring put it to the test and we have had no further leaks.(Fig 47)
-
Fig 43
-
Fig 44
-
Fig 45
-
Fig 46
-
Fig 47
Two year update[edit | edit source]
After a year of weather there were a couple of improvements that needed to be done. The first was on the retaining wall. Our original wall did not reach all the way down to the ground so a small gap was left where soil found its way through.(Fig 48) If left this could have become a great problem because it would clog up the French drain around the foundation. To fix it I just added an additional board on the bottom of the wall and made sure it was inserted into the ground about an inch so no soil could find its way through.(Fig 49) Next I decided that the ends of the rafters that were exposed on the North side needed to be covered. At first I thought they would be OK because they were stained, but I realized that with the amount of rain we get in the winter it would be better if they were covered.(Fig 50) Here I just added an additional piece of the roofing material so that it overhung the exposed ends of wood.(Fig 51) While extending the roof I discovered another problem; every screw in the roof was leaking. To fix this I backed out each screw a little bit, ran a small bead of silicon around them and tightened them back down. The silicon created a good seal and so far there have been no more leaks.
-
Fig 48
-
Fig 49
-
Fig 50
-
Fig 51
Window Update 2010[edit | edit source]
The window on the east side of the greenhouse had a number of problems which are explained above. All of these due to the fact that the window was designed to go vertical but was installed it horizontal. Eventually the weight of the glass on its side shifted the window out of its track and in a storm was blown out and broke. We decided the entire window should be replaced and found another recycled window that was meant to be on its side. So far we have not had any further problems with the new window.
See also[edit | edit source]
- Greenhouses
- Greenhouse waste heat exchange
- Construction of an Affordable Greenhouse
- Miniature greenhouses from plastic bottles