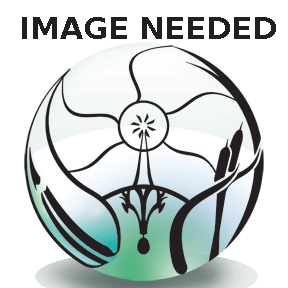
The Mechanical Arm Demo, M.A.D. demonstrates basic mechanical movement coupled with a simple design. The arm was designed in the winter of 2024 and built Spring of 2024—the motivation behind the M.A.D. was to help get more engagement and interest from the public youth. To solve this problem we came up with M.A.D. The intended users are future Engineering students considering Cal Poly Humboldt.
Background[edit | edit source]
During the Spring 2024 semester, i2 inc.‘s project for Dr. Eileen Cashman intends to provide an insight into California State Polytechnic University, Humboldt’s School of Engineering. We intend to create an attraction to be displayed at recruitment events. i2 inc. consists of members Elias Wiggins, an Environmental Resource Engineering major, Ryan Harris, an Energy Systems Engineering major, Felix Canari, a Environmental Resource Engineering major, and Evan Jefferson, a Mechanical Engineering major.
Problem statement[edit | edit source]
The objective of i2 inc. is to Design test and demonstrate a system that embodies California State Polytechnic University, Humboldt School of Engineering to garner interest in the department.
Criteria[edit | edit source]
Criteria | Weights |
cost | 6 |
portability/size | 7 |
engagement | 10 |
mechanical principles | 9 |
humboldt-ness | 8 |
Prototyping[edit | edit source]
Show examples of the prototyping process including what you learned. A great way to communicate your design your process (and to earn extra points!) is to show your early drawings (by hand and digital), failed attempts and photos of tools, materials and your team (or your hands) as you build this prototype.
Final product[edit | edit source]
For the final product decision for i^2 inc s mechanical arm, there were some changes that the team made. The final design includes a stronger material than wood, along with a smaller design to accommodate the weight and the arms. There was also a change with the claw, going from 2 prods to 3 for betting gripping strength. The figure below shows the material change and the arm pieces.
Initially, we decided to make the dimensions of the base a 12x12 inch square, however, after drafting the initial base, we realized that the square base was not good for rotating. This led to the design decision to make the base a circle with a diameter of 12 inches. The base consists of two pieces. The first base is a 12x12-inch square that has 3 gears. The first of which is 6 inches in diameter, the second is 5 inches in diameter and the last is 3 inches in diameter. On the last gear, there is a handle connecting it by a 0.112 inch screw. This handle allows for the rotation of the two big gears, thus making the arm move as well. The second base is the 12-inch diameter circle that houses the actual arm. There are slits in the circle to allow the trapezoid pieces to fall into place holding them steady. These slits act like a puzzle keeping the base in place. Attaching the Arm pieces to the base will be a 3d printed rectangle holding the hydraulics and arms together. Also connected to the arm holes, will be a bearing with the same dimensions allowing for rotation. The material of the arm pieces, base, and gears are all refined birch wood. The hydraulics of the arm consists of a pvc pipe housing containing a chamber of water with a piston able to create pressure. The end of the tube not consisting of a plunger ends in a tube running to another piston. Depressing or retracting one of the plungers causes the inverse effect on the other plunger.
Construction[edit | edit source]
A very complete description of how the final project is built. This large section should have lots of pictures. Use the Help:Images#Galleries and probably Template:Steps (e.g. Barrel O' Fun Worm Bin Instructions).
Video instructions[edit | edit source]
A good way to display a process is by making a video explaining your process. See Template:Video for information on how to add and annotate videos.
Bill of materials[edit | edit source]
Description of costs
Materials | Quantity | Unit Cost | Total Cost |
¼” plywood | 1 2ftx4ft panel | $14.94 | $14.94 |
Syringes | 6 | $6.25 | $37.50 |
Plastic tubing | 3 | $3.33 | $10 |
Popcicle sticks | 1 | $5.00 | $5.00 |
Superglue | 1 | $5.00 | $5.00 |
cardboard | - | - basically free | - basically free |
- | - | Total | $ |
Conclusion[edit | edit source]
Testing results[edit | edit source]
Not done with testing as we write this draft. To be revised on the final draft.
Lessons learned[edit | edit source]
Collaboration can be a difficult thing.
Variations in teammate's abilities can be a blessing, but also cause struggles.
Nonetheless, the efforts of i^2 were consistent and we can have confidence in the growth we have incurred from our struggles in design.
-Elias Wiggins, i^2
Next steps[edit | edit source]
Discuss any next steps for the project as it goes on into the future.
Troubleshooting[edit | edit source]
This is only how to troubleshoot basic operation. For complex issues, the solution might just say something like contact ________. It should be a table in this format:
Problem | Suggestion |
---|---|
Example issue | Example solution or suggestion |
Does not turn on | Make sure it is plugged in |
Another issue | Etc. |
Team[edit | edit source]
Introduce team and semester in the following format:
- Lonny Grafman
- Emilio Velis
- One bullet for each team member.
References[edit | edit source]