
When you fail, ask yourself: what is your original aspiration? when you succeed, ask gain: what is your original aspiration? and remain true
Academic and Professional Background[edit | edit source]
A Ph.D. candidate at the University of Lorraine studying with Dr. Hakim Boudaoud and specializing in the vibration characterization of additively manufactured composite structures with in-depth knowledge of mechanics of solid, damping of materials and structures, as well as hands-on experience in static/dynamic mechanical testing and multi-material additive manufacturing. Completed Bachelor's program in Aeronautic Engineering and Master's program in Mechanics of Materials and Structures. My passion is extending the use of additive manufacturing in composite structures and vibration.
Currently working in the research team on innovation process (ERPI, EA 3767) and the Laboratory of Microstructures and Mechanics of Materials (LEM3, UMR 7239 CNRS) of the University of Lorraine, I will also join the FAST group of Dr. Joshua M. Pearce at the Western University as a visiting graduate student.
Research Interests[edit | edit source]
- Vibration | Damping
- Additive manufacturing | Fused filament fabrication
- Composite materials | Continuous fiber reinforced structure
- Open-source hardware and software
Publications[edit | edit source]
Journal article:[edit | edit source]
- F. Xue, G. Robin, H. Boudaoud, F. A. Cruz Sanchez, and E. M. Daya, “General Methodology to Investigate the Effect of Process Parameters on the Vibration Properties of Structures Produced by Additive Manufacturing Using Fused Filament Fabrication,” JOM, Jan. 2022, doi: 10.1007/s11837-021-05051-9.
Journal article under review:[edit | edit source]
- F. Xue, G. Robin, H. Boudaoud, F. A. Cruz Sanchez, and E. M. Daya, “Optimization of vibration damping properties of additively manufactured thermoplastic polyurethane structures,” 3d printing and additive manufacturing.
Conference proceedings:[edit | edit source]
- F. Xue, G. Robin, H. Boudaoud, F. A. Cruz Sanchez, and E. M. Daya, "Characterization and optimization of the vibration properties of mono- and multi-material structures printed by fused filament fabrication," Congrès Français de Mécanique 2022.
- F. Xue, G. Robin, H. Boudaoud, F. A. Cruz Sanchez, and E. M. Daya, "Influence of layer thickness and nozzle temperature on the interlocking adhesion strength of additive manufactured multi-material interface," Solid Freeform Fabrication 2022.
- F. Xue, G. Robin, H. Boudaoud, F. A. Cruz Sanchez, and E. M. Daya, “Effect of Process Parameters on the Vibration Properties of PLA Structure Fabricated by Additive Manufacturing,” Solid Freeform Fabrication 2021. doi: 10.26153/tsw/17573.
Projects[edit | edit source]
5-axis 3D printing of continuous fiber reinforced composite structure[edit | edit source]
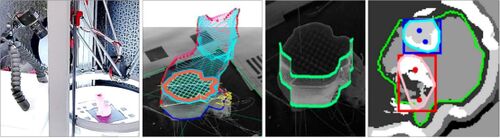
The layer-wise 3D printing analysis is built upon multiple-stage monocular image examination, which allows monitoring both the external shape of the printed object and internal structure of its layers. Starting with the side-view height validation, the developed program analyzes the virtual top view for outer shell contour correspondence using the multi-template matching and iterative closest point algorithms, as well as inner layer texture quality clustering the spatial-frequency filter responses with Gaussian mixture models and segmenting structural anomalies with the agglomerative hierarchical clustering algorithm. This allows evaluation of both global and local parameters of the printing modes.
A.L. Petsiuk, J.M. Pearce. Open source computer vision-based layer-wise 3D printing analysis. Additive Manufacturing 2020, 36, 101473. https://doi.org/10.1016/j.addma.2020.101473.
Optimization of the adhesion strength of dissimilar materials in multi-material additive manufacturing[edit | edit source]
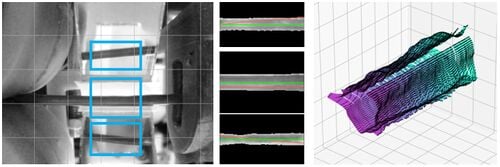
The modular system for multi-axis optical control of the diameter of the recycled 3D-printer filament makes it possible to scan part of the surface of the processed filament, save the history of measurements along the entire length of the spool, as well as mark defective areas.
A.L. Petsiuk, J.M. Pearce. Open source filament diameter sensor for recycling, winding, and additive manufacturing machines. ASME. J. Manuf. Sci. Eng. 2021, 143(10): 105001. https://doi.org/10.1115/1.4050762.
Vibration characterization of additively manufactured structures[edit | edit source]
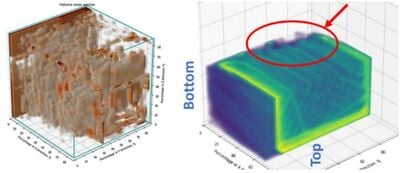
Layer-wise analysis of 3D printing quality based on histogram similarities.
Co-authors – Collaborators[edit | edit source]
Dr. Hakim Boudaoud | Dr. Joshua M. Pearce | Dr. Guillaume Robin |
Dr. Fabio Cruz. Alberto Sanchez | Prof. El Mostafa Daya |