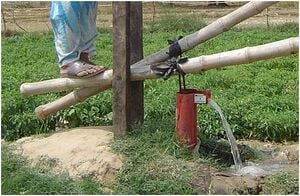
Treadle Pumps are widely used globally -- need to tie design to those that have been further developed. The treadle is a very simple design that is used to produce rotary or reciprocating motion in a machine, which dates back to Thomas Saint's original sewing machine design he had patented in 1790 and earlier. This basic component can be used in many simple machines, including grinders and pumps. A treadle pump is defined as a foot operated single acting double cylinder piston pump for low lift irrigation.[1] Pumping is activated by stepping up and down on the treadles to drive the attached pistons, creating suction in the cylinder that draws groundwater to the surface.[2] This water can be sourced from a river or well and is used for irrigating farmers' fields or to store water in a container for later use. Treadle pumps have been used in many countries worldwide such as Ghana, Zambia,[3] Swaziland, Kenya,[4] Bangladesh, Nepal, India, Cambodia and Myanmar,[5] as well as many others. Presently, 84 manufacturers now produce treadle pumps and 1.4 million have been sold to small plot Bangladeshi farmers since 1985.[6] Figure 1 below shows 12 pump designs and their origins, maximum volumetric input, features and cost.

Regional Considerations[edit | edit source]
Climate[edit | edit source]
Climate is not a big issue as it is different for each country but both temperature and pressure affect the NPSHa. Both temperature and pressure are affected both by altitude, while temperature is also affected by proximity to the equator. Climate is a factor in the developmental need for treadle pumps, as their implementation has been as a result of a growing season followed by a prolonged dry season where water can be found in abundance under the soil, but is not readily available above ground.
Engineering Principles[edit | edit source]
How They Work[edit | edit source]
A treadle pump is a basic cylinder-based pump: it comprises a cylinder fitted with a piston and some means of pushing the piston up and down.[8]A pipe connects the water source to the pump, where a non-return valve is fitted to allow water to flow in and prevent it from flowing out. The piston itself must have a snug fit inside the cylinder in order to create a vacuum to draw water in. The piston itself contains a similar valve such that, when it is forced downward by the treadle, water flows through the piston from the space below to the space above it. The opposite then occurs when the piston is lifted: the valve closes, forcing the water above the piston to the outlet all the while drawing in water from below. Various types of non-return valves are used, including rubber flaps, swinging gates and poppet valves.[9] An illustrated version of this is shown in Figure 2, and an animated version can be found at.
In the past, these pumps were hand-operated and quite inefficient, as the effort required to lift small amounts of water was significant. Using the larger muscles in one's legs and two pistons has greatly increased the efficacy of this machine. The treadles are joined, either by a rope passing over a pulley, a chain and rocker system, or a centre shaft.[10] This connects the two pistons as well and associates the upward motion of one treadle/piston with the downward motion of the other.

This pump currently has two monikers, each defined by the outlet portion of the pump. If the water is discharged to an open channel for irrigation, it is termed a suction pump. Suction pumps are designed for lifting large volumes of water from relatively shallow water sources.[13] If the water is discharged to a pipe, it is termed a pressure pump. In the pressure pump, another valve is used at the discharge end, maintaining pressure in the pipe that can be used to drive sprinklers or drippers or deliver water to a header tank.[14]
Hydraulics[edit | edit source]
A vacuum is created when the piston moves up in the cylinder and atmospheric pressure is then used to propel the water into the cylinder. Both temperature and pressure have an effect on the atmospheric pressure and the suction lift that can be obtained. In centrifugal pumps it is common to refer to the NPSHa, which is the net positive suction head available. In the treadle pump case, since the pump is located above the water source, the difference in elevation between the water and the pump is taken as positive and NPSHa decreases as the difference increases. The equation for calculating NPSHa is::[15]

Where:
P_atm = atmospheric (or absolute) pressure; γ = specific weight of the fluid; h_z = vertical distance (elevation) between the surface of the water and the pump; ∆h_f = head loss due to major and minor losses in the suction pipe, valves and fittings; P_v = vapour pressure of the fluid; and
The equation for calculating the specific weight of the fluid (water) is:[16]

Where:
ρ = density of the fluid; and g = acceleration of gravity.
NB: Density varies with altitude, acceleration of gravity with latitude.
Statics[edit | edit source]
The force applied by the person on the treadle is based on the lever principle. Operators of the pump can move their position on the treadles to gain a mechanical advantage while maintaining a comfortable applied force and steady cadence.[17]There are three types of levers: in the class I lever, the applied force and the load are on either side of the fulcrum, while the class II lever the load is positioned between the applied force and the fulcrum and the class III lever has the applied force positioned between the fulcrum and the load. The Swiss Concrete Pedal Pump (SCPP), developed by W-3-W Association Switzerland, is prime example of a class I lever (Figure 3). Tests conducted at the Lucerne School of Engineering and Architecture (HTA) showed a very impressive 65% energy efficiency and a maximum discharge volumetric flow rate of 80 L/min (with an average human input of 60 – 65 W and a suction lift of 3 m).[18]

Another example of a class I lever treadle pump is the original version developed in Bangladesh in the early 1980's, pictured below (Figure 4):
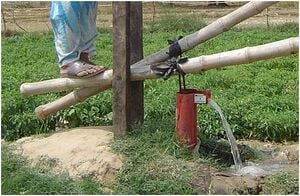
Note that if the operator were to switch sides (i.e. pump from the right of the image), Figure 4 would then become an example of a class II lever in action.
A good example of a class II lever treadle pump is the New Dawn Engineering Treadle Pump (Figure 5):
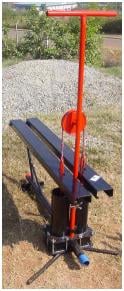
The equation that dictates the mechanical advantage of a lever is:

Where:
l = the distance between the force applied and the fulcrum; and r = the distance between the load and the fulcrum.
When the foot force of an operator is directed precisely on top of the pistons as shown in Figure 6-1 below, this force is transferred directly to the pistons. As the caption to the right of the image demonstrates, this is equal to a mechanical advantage (MA) of 1. However, as the operator moves along the treadles, an MA can be obtained in one of two ways: Figure 6-2 shows an increased distance between the applied force and the fulcrum (class II lever), hence an MA greater than 1 and a mechanical advantage gained in force. Figure 6-3 shows a decrease in the distance between the applied force and the fulcrum (class III lever), hence an MA less than 1 and a mechanical advantage gained in speed and range of motion. What this means is that a light operator, such as a child, could operate the pump standing farther away from the pivot (to take advantage of the extra leverage), and a heavy, or strong operator could move closer to the pivot with both being comfortable pumping positions.[22]Mechanical advantage has a direct impact on the stroke length of the piston: an MA greater than 1 means a decrease in stroke length while an MA less than 1 results in an increase in stroke length. Taking advantage of MA's greater than 1 allows more force to be applied to the piston, hence greater pumping pressures can be achieved, but this is at the expense of volumetric flow because of the reduced piston stroke length.[23]

Fabrication[edit | edit source]
Components[edit | edit source]
It is noted that the following materials are typically used in field applications of the treadle pump. However, with the use of a 3-D printer, most components can be made at minimal cost to the operator. For example, the pump's cylinders, manifold, pistons (excluding cups/rings), piston rods and the pulley wheel can all be made with a 3-D printer of sufficient size. The only "specialty" parts the treadle pump is left with are the non-return valves and the piston cups/rings, as the treadles and the base can be made of locally sourced wood or bamboo.
Pump Cylinders[edit | edit source]
Treadle pumps make use of two cylinders (one per treadle), with an average cylinder diameter of 100 mm and a normal range of diameters between 75 mm (for high heads) and 150 mm (for low heads),.[25][26] A cylinder of diameter 100 mm is capable for pumping water to heads of between 3 and 8 m.[27] Materials used include curved steel sheet, bamboo, PVC pipe and concrete,.[28][29] The material used varies widely based on availability of the materials, availability of skilled workers, type of pump (suction vs. pressure – bamboo is considered unsuitable for pressure pump applications) and cost. The choice of material will also be influenced by the type of pump manifold and how it connects to the cylinders.[30]
Pump Manifold[edit | edit source]
The manifold connects the inlet and outlet pipes to the cylinders, as well as housing the non-return valves (two in a suction pump and three in a pressure pump). Due to the nature of the outlet of a suction pump, there is no need for the outlet side. It is necessary that the design of the manifold take into consideration the removal of the non-return valves for maintenance. The manifold is most likely a steel box, but can be made of concrete as well, as in the Swiss design (Figure 3). It can also be made from, in a pump with PVC cylinders, pipe fittings or straight pipe.
Piston Assembly[edit | edit source]
The pistons travel up and down within the cylinder, and it is important that they remain vertical in the cylinder as the treadles are moved up and down; this is done to maintain a good seal between the piston and the walls of the cylinder. The piston rod is thus connected to the treadle via a hinged joint. Piston rods are generally made of round steel bar, as it is a very robust material and is usually available. The pistons themselves can be made of wood, plastic, or steel as well, with leather or rubber cups or rings to form the seal with the cylinders.[31]The piston cups or rings must themselves also be robust; they must sustain the rigours of continual friction against the cylinder wall.[32]
Non-Return Valves[edit | edit source]
It has been mentioned previously that suction pumps have two non-return valves and pressure pumps have three. The valves allow water to flow in one direction only, by opening and closing due to the positive and negative pressures developed during pumping. It is possible for another valve to be fitted at the entrance to the inlet pipe, which would avoid the need to re-prime the pump every time it is used,[33]as well as preventing large pieces of dirt from getting sucked into the pump system. Various types of non-return valves are used, including rubber flaps, swinging gates and poppet valves.[34]
Treadles[edit | edit source]
Treadles need to be strong enough to take the forces applied by the operator, and stiff enough to transfer the applied forces to the pistons without undergoing significant bending. Depending on the lever class being used, the treadles can be hinged at one end or in the middle, with the opposite end being supported by a rope and pulley or rocking bar. The range of movement is dictated by the stroke length of the pistons and by the comfortable working step of the operator. Treadles are generally made from wood, bamboo or steel. Steel is the stiffest and most expensive of these materials; however, the mechanical advantage can be greatest when using steel treadles. There is a practical upper limit to this advantage, as the pump may overturn if the operator stands at the extreme end of the treadles and there isn't enough weight in the frame.[35]
Pulley Wheel or Rocking Bar[edit | edit source]
The rope and pulley wheel enable the reciprocal movement of the treadles. The wheel has a central axle mounted to a frame; a simple axle, such as a 16 mm diameter bolt, is normally used.[36] It is usually made of wood soaked in oil to preserve it and to lubricate the movement.[37]The alternative to the rope and pulley method is the rocking bar. This arrangement is harder to balance but may be easier to construct in some cases.[38]
Frame[edit | edit source]
The components of the treadle pump are mounted on a frame which can be firmly embedded in the ground; it can also provide support for the operator. Figure 4 and Figure 5 above show examples of a frame that is meant to support the operator. As well, they show examples of wood and bamboo being used as a frame (Figure 4), or steel (Figure 5). The Swiss design (Figure 3) shows a frame whose base is encased in concrete. The steel and concrete frames can easily stand up to the rigours of continual use but are much more expensive and much less portable than their wood or bamboo counterparts. Figure 7 illustrates the basic components of the treadle pump below.

Desirable Features[edit | edit source]
Figure 8 below, taken from Kay, 2000,[40]identifies most of the desirable characteristics for a treadle pump. Since the operator's position on the treadles can vary, this is not explicitly defined in the table. Other desirable characteristics can include weight, or lack thereof: a heavy base and frame can be left alone as they are more difficult to steal, while a wooden or bamboo frame are light and portable, so can be used in several areas of one farmer's field, or can be shared by neighbouring farmers to irrigate the collective land.
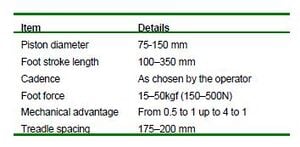
Tools, Skills and Knowledge Required[edit | edit source]
Step-by-step manufacturing and installation instructions can be found here for manufacturing a concrete based treadle pump:
As well, the Development Technology Unit from the Department of Engineering at the University of Westwick in England put out a paper detailing the constructions methods used as well as performance characteristics for the Bellow Pump (not a true treadle pump), the Tapak-Tapak or Bangladesh Pump, the USAID Treadlepump (Ivory Coast), the Harare Treadlepump (Zimbabwe) and the Warwick Treadlepump (Nigeria).
Technical Specifications[edit | edit source]
For the above W3W concrete pedal pump, some general information and a summary of the pump's capabilities can be found at:
Figure 9 below shows the main dimensions of four treadle pumps currently in use in Zimbabwe.
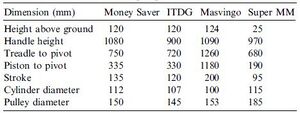
Estimated Costs[edit | edit source]
In Africa, costs vary, but on average, they(the pressure delivery variation of the Bangladesh pump) are about $100 each if spare parts, fixings and suction, and delivery hoses are included. The specific feature of the pump designed by SE3WE is that the cylinders are encased in a concrete block to protect them and to reduce the need for skilled metal workers.[43]
Possible Routes to Optimization[edit | edit source]
Good performance depends on generously sized valves and passages (to reduce head losses), good seals and fast closing valves (to reduce internal and external leakage), correct gearing (to allow users to choose ergonomically efficient cadences and strokes) and smooth, well-lubricated linkages (to raise mechanical efficiency)[44] As well, simply adjusting the shape of the piston head would greatly reduce fluid friction during its downstroke.
References[edit | edit source]
- ↑ New Dawn Engineering. (2009). Treadle Pump for Low Lift Irrigation. Retrieved April 4, 2010, from New Dawn Engineering: http://www.newdawnengineering.com/website/pumps/treadle/
- ↑ International Development Enterprises. (2010). Treadle Pump. Retrieved April 14, 2010, from International Development Enterprises: http://www.ideorg.org/OurTechnologies/TreadlePump.aspx
- ↑ Engineers Without Borders Canada. (n.d.). The Treadle Pump. Retrieved April 4, 2010, from Engineers Without Borders Canada: http://www.ewb.ca/en/whatwedo/overseas/projects/treadle.html
- ↑ New Dawn Engineering. (2009). Treadle Pump for Low Lift Irrigation. Retrieved April 4, 2010, from New Dawn Engineering: http://www.newdawnengineering.com/website/pumps/treadle/
- ↑ Cooper Hewitt. (2006). Bamboo Treadle Pump. Retrieved April 4, 2010, from Design for the Other 90%: http://web.archive.org/web/20141020235501/http://other90.cooperhewitt.org:80/Design/bamboo-treadle-pump
- ↑ International Development Enterprises. (2010). Treadle Pump. Retrieved April 14, 2010, from International Development Enterprises: http://www.ideorg.org/OurTechnologies/TreadlePump.aspx
- ↑ Food and Agriculture Organization, United Nations. (2002, January). Briefing Note on Treadle Pumps. Retrieved April 4, 2010, from Water Conservation and Use in Agriculture: http://www.wca-infonet.org/servlet/BinaryDownloaderServlet?filename=1016103720274 Treadlepump brief.pdf&refID=18556
- ↑ Kay, T. B. (2000). Treadle pumps for irrigation in Africa. International Programme for Technology and Research in Irrigation and Drainage. Rome: Food and Agriculture Organization of the United Nations.
- ↑ Development Technology Unit. (1991). The Treadle Pump: Working Paper No. 34. Development Technology Unit, Department of Engineering. Coventry: University of Warwick.
- ↑ Kedge, C. (2001). The Introduction of Treadle Pumps into South Africa. (p. 8). Johannesburg: SABI.
- ↑ Kedge, C. (2001). The Introduction of Treadle Pumps into South Africa. (p. 8). Johannesburg: SABI.
- ↑ Kay, T. B. (2000). Treadle pumps for irrigation in Africa. International Programme for Technology and Research in Irrigation and Drainage. Rome: Food and Agriculture Organization of the United Nations.
- ↑ Kedge, C. (2001). The Introduction of Treadle Pumps into South Africa. (p. 8). Johannesburg: SABI.
- ↑ Kay, T. B. (2000). Treadle pumps for irrigation in Africa. International Programme for Technology and Research in Irrigation and Drainage. Rome: Food and Agriculture Organization of the United Nations.
- ↑ NPSH - Net Positive Suction Head. (2005). Retrieved April 16, 2010, from The EngineeringToolBox: http://www.engineeringtoolbox.com/npsh-net-positive-suction-head-d_634.html
- ↑ Density, Specific Weight and Specific Gravity. (2005). Retrieved April 16, 2010, from The EngineeringToolBox: http://www.engineeringtoolbox.com/density-specific-weight-gravity-d_290.html
- ↑ Kay, T. B. (2000). Treadle pumps for irrigation in Africa. International Programme for Technology and Research in Irrigation and Drainage. Rome: Food and Agriculture Organization of the United Nations.
- ↑ Water for the Third World. (2006). Scientific testing proves efficiency. Retrieved April 4, 2010, from Water for the Third World: http://www.w-3-w.org/index2.html
- ↑ Water for the Third World. (2006). Scientific testing proves efficiency. Retrieved April 4, 2010, from Water for the Third World: http://www.w-3-w.org/index2.html
- ↑ International Development Enterprises. (2010). Treadle Pump. Retrieved April 14, 2010, from International Development Enterprises: http://www.ideorg.org/OurTechnologies/TreadlePump.aspx
- ↑ New Dawn Engineering. (2009). Treadle Pump for Low Lift Irrigation. Retrieved April 4, 2010, from New Dawn Engineering: http://www.newdawnengineering.com/website/pumps/treadle/
- ↑ Kay, T. B. (2000). Treadle pumps for irrigation in Africa. International Programme for Technology and Research in Irrigation and Drainage. Rome: Food and Agriculture Organization of the United Nations.
- ↑ Kay, T. B. (2000). Treadle pumps for irrigation in Africa. International Programme for Technology and Research in Irrigation and Drainage. Rome: Food and Agriculture Organization of the United Nations.
- ↑ Kay, T. B. (2000). Treadle pumps for irrigation in Africa. International Programme for Technology and Research in Irrigation and Drainage. Rome: Food and Agriculture Organization of the United Nations.
- ↑ Kay, T. B. (2000). Treadle pumps for irrigation in Africa. International Programme for Technology and Research in Irrigation and Drainage. Rome: Food and Agriculture Organization of the United Nations.
- ↑ Development Technology Unit. (1991). The Treadle Pump: Working Paper No. 34. Development Technology Unit, Department of Engineering. Coventry: University of Warwick.
- ↑ Development Technology Unit. (1991). The Treadle Pump: Working Paper No. 34. Development Technology Unit, Department of Engineering. Coventry: University of Warwick.
- ↑ Kay, T. B. (2000). Treadle pumps for irrigation in Africa. International Programme for Technology and Research in Irrigation and Drainage. Rome: Food and Agriculture Organization of the United Nations.
- ↑ Development Technology Unit. (1991). The Treadle Pump: Working Paper No. 34. Development Technology Unit, Department of Engineering. Coventry: University of Warwick.
- ↑ Development Technology Unit. (1991). The Treadle Pump: Working Paper No. 34. Development Technology Unit, Department of Engineering. Coventry: University of Warwick.
- ↑ Kay, T. B. (2000). Treadle pumps for irrigation in Africa. International Programme for Technology and Research in Irrigation and Drainage. Rome: Food and Agriculture Organization of the United Nations.
- ↑ Development Technology Unit. (1991). The Treadle Pump: Working Paper No. 34. Development Technology Unit, Department of Engineering. Coventry: University of Warwick.
- ↑ Kay, T. B. (2000). Treadle pumps for irrigation in Africa. International Programme for Technology and Research in Irrigation and Drainage. Rome: Food and Agriculture Organization of the United Nations.
- ↑ Development Technology Unit. (1991). The Treadle Pump: Working Paper No. 34. Development Technology Unit, Department of Engineering. Coventry: University of Warwick.
- ↑ Kay, T. B. (2000). Treadle pumps for irrigation in Africa. International Programme for Technology and Research in Irrigation and Drainage. Rome: Food and Agriculture Organization of the United Nations.
- ↑ Development Technology Unit. (1991). The Treadle Pump: Working Paper No. 34. Development Technology Unit, Department of Engineering. Coventry: University of Warwick.
- ↑ Kay, T. B. (2000). Treadle pumps for irrigation in Africa. International Programme for Technology and Research in Irrigation and Drainage. Rome: Food and Agriculture Organization of the United Nations.
- ↑ Development Technology Unit. (1991). The Treadle Pump: Working Paper No. 34. Development Technology Unit, Department of Engineering. Coventry: University of Warwick.
- ↑ Kay, T. B. (2000). Treadle pumps for irrigation in Africa. International Programme for Technology and Research in Irrigation and Drainage. Rome: Food and Agriculture Organization of the United Nations.
- ↑ Kay, T. B. (2000). Treadle pumps for irrigation in Africa. International Programme for Technology and Research in Irrigation and Drainage. Rome: Food and Agriculture Organization of the United Nations.
- ↑ Kay, T. B. (2000). Treadle pumps for irrigation in Africa. International Programme for Technology and Research in Irrigation and Drainage. Rome: Food and Agriculture Organization of the United Nations.
- ↑ Chigerwe, J. et al. (2004). Low head drip irrigation kits and treadle pumps for smallholder farms in Zimbabwe: a technical evaluation based on laboratory tests. Physics and Chemistry of the Earth, 1049-1059.
- ↑ Food and Agriculture Organization, United Nations. (2002, January). Briefing Note on Treadle Pumps. Retrieved April 4, 2010, from Water Conservation and Use in Agriculture: http://www.wca-infonet.org/servlet/BinaryDownloaderServlet?filename=1016103720274_Treadlepump_brief.pdf&refID=18556
- ↑ Thomas, T. H. (1993). The Performance Testing of Treadle Pumps. Development Technology Unit, Department of Engineering. Coventry: University of Warwick.
Bibliography[edit | edit source]
- Chigerwe, J. et al. (2004). Low head drip irrigation kits and treadle pumps for smallholder farms in Zimbabwe: a technical evaluation based on laboratory tests. Physics and Chemistry of the Earth, 1049-1059.
- Cooper Hewitt. (2006). Bamboo Treadle Pump. Retrieved April 4, 2010, from Design for the Other 90%: http://web.archive.org/web/20141020235501/http://other90.cooperhewitt.org:80/Design/bamboo-treadle-pump
- Density, Specific Weight and Specific Gravity. (2005). Retrieved April 16, 2010, from The EngineeringToolBox: http://www.engineeringtoolbox.com/density-specific-weight-gravity-d_290.html
- Development Technology Unit. (1991). The Treadle Pump: Working Paper No. 34. Development Technology Unit, Department of Engineering. Coventry: University of Warwick.
- Engineers Without Borders Canada. (n.d.). The Treadle Pump. Retrieved April 4, 2010, from Engineers Without Borders Canada: http://www.ewb.ca/en/whatwedo/overseas/projects/treadle.html
- Food and Agriculture Organization, United Nations. (2002, January). Briefing Note on Treadle Pumps. Retrieved April 4, 2010, from Water Conservation and Use in Agriculture: http://www.wca-infonet.org/servlet/BinaryDownloaderServlet?filename=1016103720274_Treadlepump_brief.pdf&refID=18556
- International Development Enterprises. (2010). Treadle Pump. Retrieved April 14, 2010, from International Development Enterprises: http://www.ideorg.org/OurTechnologies/TreadlePump.aspx
- Kay, T. B. (2000). Treadle pumps for irrigation in Africa. International Programme for Technology and Research in Irrigation and Drainage. Rome: Food and Agriculture Organization of the United Nations. http://www.wca-infonet.org/servlet/CDSServlet?status=ND0yNjkwLjMwMDgmNj1lbiYzMz1kb2N1bWVudHMmc2hvd0NoaWxkcmVuPXRydWUmMzc9aW5mbw~~#koinfo
- Kedge, C. (2001). The Introduction of Treadle Pumps into South Africa. (p. 8). Johannesburg: SABI. http://www.wca-infonet.org/servlet/BinaryDownloaderServlet?filename=documents/7963.The_introduction_of_treadle_pumps.pdf&refID=7963
- New Dawn Engineering. (2009). Treadle Pump for Low Lift Irrigation. Retrieved April 4, 2010, from New Dawn Engineering: http://www.newdawnengineering.com/website/pumps/treadle/
- NPSH - Net Positive Suction Head. (2005). Retrieved April 16, 2010, from The EngineeringToolBox: http://www.engineeringtoolbox.com/npsh-net-positive-suction-head-d_634.html
- Thomas, T. H. (1993). The Performance Testing of Treadle Pumps. Development Technology Unit, Department of Engineering. Coventry: University of Warwick. http://www.wca-infonet.org/servlet/BinaryDownloaderServlet?filename=1010154241527_wp39.pdf&refID=12940
- Water for the Third World. (2006). Scientific testing proves efficiency. Retrieved April 4, 2010, from Water for the Third World: http://www.w-3-w.org/index2.html